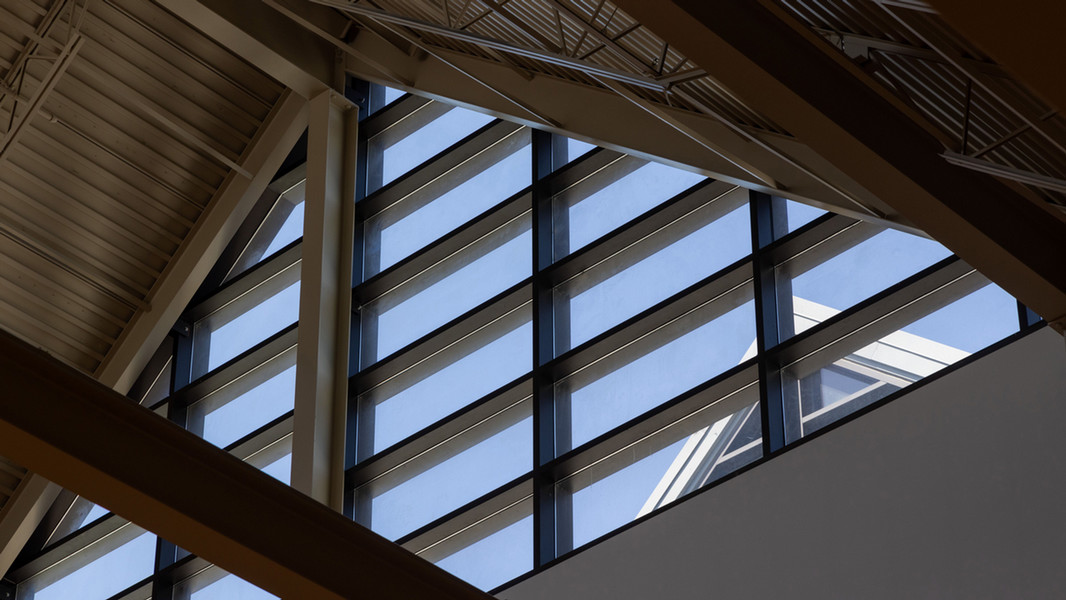
Environmental Health and Safety
Lock Out / Tag Out (LOTO) Plan
1. Purpose
- This procedure establishes the minimum requirements for the lockout/tagout of energy-isolating devices whenever maintenance or servicing is done on a machine or piece of equipment. It ensures that the machine or equipment is stopped and isolated from all potentially hazardous energy sources and locked out before employees begin to perform any servicing or maintenance where the unexpected energizing or start-up of the machine or equipment or release of stored energy could cause injury.
- Whenever major replacement, repair, renovation, or modification of a machine or equipment is performed, and whenever new machines or equipment are installed, energy isolating devices for such machines or equipment shall be designed to accept a lockout device [WAC 296-803-300].
2. Compliance
- Whenever it becomes necessary to perform maintenance, service, replacement, or repair on a piece of equipment, all procedures in this chapter are to be followed to isolate it from the energy source.
- Upon observing a machine or piece of equipment which is locked out or tagged out, no attempt shall be made to start, energize or use that machine or piece of equipment.
- It is expressly forbidden for any person, other than a supervisor upon review or the one installing a red tag or lockout, to remove the lockout or red tag or activate the tagged power panel or piece of power equipment. Failure to follow this procedure could result in serious damage, injury, and/or loss of life. It will be considered an extremely serious safety violation if a lockout device or tagout warning is bypassed, overridden, or ignored.
3. Procedures
- Persons working on powered or pressurized (p/p) equipment may be subject to serious injury or death due to unexpected operation of the equipment. Positive controls must be established and enforced to assure safe work around such equipment. The two energy sources that are of most concern are electricity and steam.
- Exception:
- The lockout/tagout procedures are not required when all of the following conditions are met:
- Work is being performed on p/p equipment in limited-access locations
away from other workers; and - The location of the power shut-off device remains within the sight of the person performing the work; and
- The person performing the work will not leave the equipment until the work is completed.
- Work is being performed on p/p equipment in limited-access locations
- These conditions generally apply to persons performing maintenance or repairs of a short-term nature. Whenever one of these conditions cannot be met, the following standard lockout/tagout procedures must be followed.
- Electrical Procedures
- Notification – Advise affected persons (building monitor, department head, etc.) and appropriate supervisor(s) as far in advance as possible. This should be done for situations such as major power outages, significant HVAC changes, power outages to areas with computers, etc.
- Identify all power outages
- Turn off all power sources
- Place tag/padlock on the control or master switch
- Each lock must be tagged with the name of the person performing the work, the description of the work, the date, and the department performing the work. Locks and tags are available from supervisors. If more than one person is working on the equipment, each worker must place their own lock and tag on the control or switch. If the control or switch is always in sight, the worker may choose to just tag the control or switch.
- Exception - If the power source does not have a lockout capability, it must be disconnected and tagged.
- Verifying – Before starting work, make sure that equipment cannot be set in motion or energized by alternate sources, etc.
- Removal – When the job is finished, each worker shall remove their lock(s) and tag(s); one worker must not remove the lock or tag of another worker. In some circumstances, supervisors may need to remove or grant permission to remove a worker's lock or tag. This may only be done after a thorough inspection has been made of the area, by the supervisor or their representative, to assure that no person will be exposed to dangers as a result of activating the system. The supervisor will ensure that the person whose name is on the lock or tag is contacted and notified that their lock or tag is being or has been removed.
- Keys – Each padlock will have only one key and a master, which shall be retained by the supervisor. If a key is lost, report it immediately to the supervisor.
- Pressurized Lines Procedures
- Notification - Advise affected persons (building monitor, department head, etc.) and appropriate supervisor(s) as far in advance as possible. This should be done for situations such as major power outages, significant HVAC changes, power outages to areas with computers, etc.
- Identify All Sources of Pressure to the Area
- Locate all pressure lines connected to the line being worked on.
- Close and Lock-out Control Valve(s)
- Any section being worked on must be verified that it is double isolated by checking both valves (the one immediately preceding the “T” and the one following) to ensure that they are both securely in the off position.
- Place Tag/Padlock on the Control or Master Switch
- Each lock must be tagged with the name of the person performing the work, the description of the work, the date, and the department performing the work. Locks and tags are available from supervisors. If more than one person is working on the equipment, each worker must place their own lock and tag on the control or switch. If the control or switch is always in sight, the worker may choose to just tag the control or switch.
- Exception - If the power source does not have a lockout capability, it must be disconnected and tagged.
- Verifying – Before starting work, make sure that the line cannot be energized by an alternate source.
- Bleed the Line
- Long-Term Shut Downs – For the long-term closure of a line, the use of a blank flange between the power source and the job should be considered.
- Upon Completion – When the job is finished, remove the blank flange and open valves as appropriate. Then follow procedure 3.3.8 above.
- The lockout/tagout procedures are not required when all of the following conditions are met:
CWU News

Online Master’s of Education program now offers special education endorsement
May 15, 2024
by Rune Torgersen

Lenny Price brings Detroit perspective to CWU Jazz
May 15, 2024
by University Relations