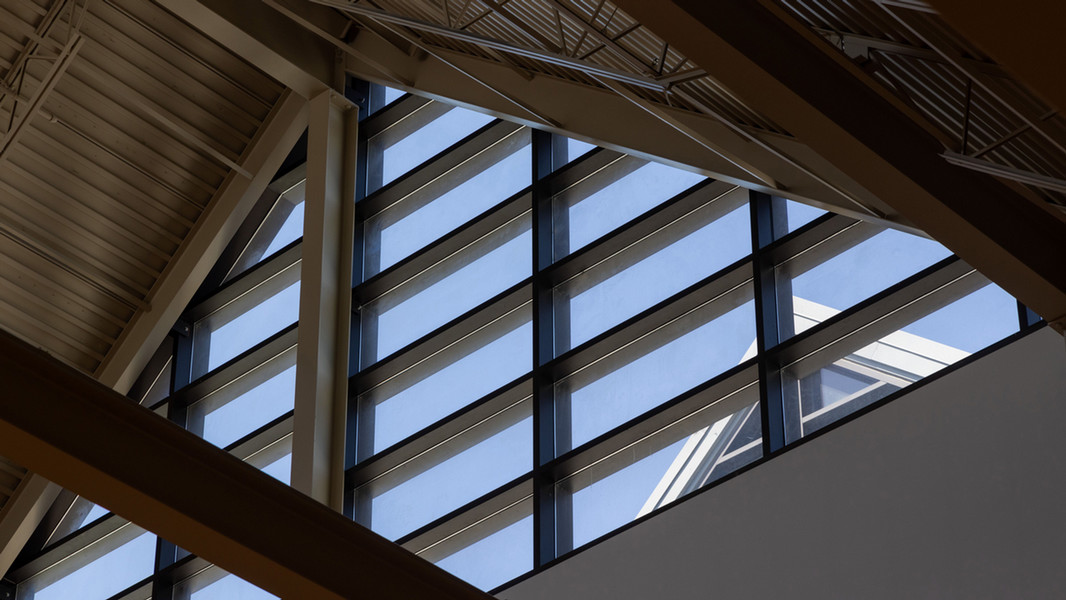
Environmental Health and Safety
Standard Operating Procedures (SOP)
-
CWU SOP Policy
- Standard Operating Procedures (SOPs)
- Laboratories must provide employees with standard operating procedures (SOPs) to be followed when laboratory work involves the use of hazardous substances or procedures. The SOPs must address all requirements to perform the laboratory procedures safely. The requirements may either be stated in a cover sheet attached to the laboratory protocol(s) or be integrated into a protocol. The requirements are described in this section of the manual.
- For advice in developing SOPs, call EH&S at 509-963-2255 or email EHS@cwu.edu.
- SOP Components
- Required Components: The required elements are listed below. If you would like to compare an SOP received from another organization to the requirements, SOPs must address the following items:
- Process Identification: Identify the chemicals, process or equipment involved. If there is any question as to the chemicals produced in the process, you should consider identifying the stock chemicals, intermediates, final compounds and wastes involved, and such factors as use of catalysts, inert compounds, heat, cold, and varied operating pressures which are involved in the process.
- Controls: List required methods to control potential exposures, including:
- Use of engineering controls. Engineering controls provide a permanent means of protection and are preferred over other types of controls. Some examples of engineering controls are working in an area with good ventilation (e.g., ducted exhaust from equipment, fume hoods or glove boxes), storing particularly hazardous chemicals in locked cabinets, and using built-in barriers to restrict access to the area or to protect from potentially explosive situations.
- Use of administrative controls, i.e., specific safe practices such as keeping the fume hood sash as low as possible, storing chemicals with secondary containment, substituting pre-formulated liquids instead of powders to be weighed and prepared, hygiene practices such as hand washing, and procedures for removal and disposal of contaminated PPE.
- Use of personal protective equipment (PPE) such as gloves, lab coats, what extremities need coverage, etc., which is the least preferred method of protection if alternatives are available. However, when PPE is required, the PPE must be specified completely, such as the type of glove to be used and whether it is necessary for the entire process or at certain steps.
- Equipment Checks: Describe ways to verify that the fume hood and other control system(s) are operating correctly, before using hazardous chemicals.
- Potentially Hazardous Situations: Provide guidance for handling spills and identifying if a spill is causing a hazardous situation. For example, laboratory personnel may be able to safely handle a spill of a liter of dilute acid anywhere in the laboratory, but may need to evacuate if 100 milliliters of a toxic chemical is spilled outside a fume hood. This also provides guidance when purchasing a chemical, as to the maximum size of container.
- Waste Management: Identify safe disposal methods for routinely generated wastes. This includes describing procedures to neutralize or treat wastes to make handling safer or to reduce the amount of hazardous waste.
- Particularly Hazardous Substances: Provide additional details if “particularly hazardous substances” (highly toxic or dangerous chemicals, carcinogens, reproductive toxicants or select toxins) are used. These additional details should address using specific containment device(s) such as fume hoods or glove boxes, providing authorizations for using the particularly hazardous substance(s), describing additional procedures for decontamination and safely handling contaminated waste materials, and establishing a designated area for the procedure.
- Authorizations: Describe any requirements for obtaining authorization before being allowed to perform the procedure, operation or activity. An example could be that a worker must have training documented before performing a certain procedure for the first time. Other required authorizations could include completing a medical examination before using a respirator when performing procedures involving certain hazardous substances (e.g., lead dust, pathological organisms). Authorizations should be required before a person could independently perform a process using particularly hazardous substances.
- Appearance:
- SOPs obtained from other organizations and SOPs written in the form of step-by-step procedures can be used as long as all the basic components are addressed and as long as the SOP accurately describes your laboratory’s safety requirements. Follow the guidelines in B.1., to make it easier to assure that all the safety elements needed in the SOP have been addressed. If SOPs are provided by outside sources (such as equipment suppliers or another laboratory) or modified from a template, they must be carefully reviewed to ensure they describe your protective measures accurately, including describing specific types of PPE and control equipment you will use.
- The traditional SOP form described in this section is meant to be attached as a cover sheet to a laboratory protocol or “cookbook” collection of protocols. This standardized SOP form has been used historically at the Central Washington University and other institutions. It addresses all required components. The forms in Figure 1-1 and Figure 1-2 at the end of this section provide explanation of the elements. An electronic, blank form is available at S:\Chemistry\Safety\SOPs.
- If using the standardized SOP form, all sections must be completed for each process, class of chemicals, or individual chemical. For “particularly hazardous substances” (acute toxicants, highly dangerous chemicals, carcinogens, mutagens, teratogens), the 8 basic elements need to be expanded, and 3 more elements, 9 through 11, must be completed.
- Feel free to attach additional information, such as Material Safety Data Sheets (MSDSs) or Safety Data Sheets (SDSs) to your SOP. Chemical-specific hazard information is available in the appendices of certain regulations (such as for arsenic and lead), the UCLA and UW EH&S web pages, other web sites, and reference books. An example of this additional information is attached to the Example Benzene SOP in this manual.
- Required Components: The required elements are listed below. If you would like to compare an SOP received from another organization to the requirements, SOPs must address the following items:
- Example Generic SOPS
- Example and generic SOPs are available on the EH&S web site. If used by your laboratory, these examples must be modified and customized as necessary to make them specific to your laboratory conditions. If your laboratory generates an SOP we highly encourage you to make it available to other labs, please send an electronic copy to your department safety officer.
- SOP Development
- To develop your laboratory SOPs, EH&S suggests the following steps
- Step 1 – Modify Existing SOPs: EH&S recommends you review and modify any generic SOPs that pertain to your laboratory. This allows you to become familiar with the required elements, as described on the attached SOP forms (Figures 1-1 and 1-2).
- Step 2 – Identify Requirements: Identify if any particularly hazardous substances are in use in your laboratory, and identify which way of writing your SOPs will best cover your laboratory’s chemicals or processes. SOPs can be written in one or more of the following ways:
- By Process
- By process, such as distillation, peptide synthesis, or gel electrophoresis.
- Safety requirements could be noted either by integrating them into the steps in the process or by using a “cover sheet” of safety requirements for the process. If hazardous intermediates are created, carefully consider if there are specific precautions which should be noted, such as how to tell if a release or spill occurs, what symptoms may develop if a person is exposed, and any special precautions for spill clean-up and waste disposal.
- By Individual Chemical
- By each individual chemical, such as acrylamide, formaldehyde, or toluene
- This approach may be most useful if a limited number of hazardous substances are used in the laboratory or if using a particularly hazardous substance.
- By Class of Chemical:
- By class of chemicals, such as mineral acids, organic solvents or peroxidizable chemicals.
- This approach may be most useful if a number of similar procedures are performed using similar substances.
- By Process
- Step 3 – Complete the SOPs
- After modifying generic SOPs and identifying which ways of writing are most useful in your situation, continue by developing SOPs for processes, chemicals and chemical classes not previously written. Ensure all elements of the SOPs are addressed if the SOP pertains to chemicals considered particularly hazardous (those that have a high degree of acute toxicity, are especially dangerous or are select carcinogens or reproductive toxins, and similar substances).
- Step 4 – File the SOPs
- After completing the SOPs, file the master copies in your laboratory Chemical Hygiene Plan so that everyone in your lab can find them. If they are not physically filed in the laboratory- specific information section of your CHP, the laboratory-specific information pages should be annotated to identify where the SOPs are physically located in your lab.
- Distributing Copies of the SOPs
- If you provide working copies of your SOPs to your staff, keep track of how many copies you made and distributed. When you make changes, you will need to assure that the up-dated SOPs reach all those who perform the procedures.
- If you develop an SOP which you believe can be used by other departments in the University, please forward a copy electronically to ehs@cwu.edu.
- Update SOPs as Needed
- If you note changes to your process or chemical use which impact an SOP, or recognize improvements that can be made to the SOP, update it as soon as it is convenient. Note the revision date on the SOP.
- Notify all lab personnel of the revised SOP and train them on the updated SOP accordingly. Replace the previous SOP in your Chemical Hygiene Plan files and anywhere else they may have been placed, including the working copies which would be referred to on a daily basis by your staff and those which may be kept at the lab benches or in individual staff members’ files.
- To develop your laboratory SOPs, EH&S suggests the following steps
- Standard Operating Procedures (SOPs)
-
Acutely Toxic Chemical SOP
Description
It is the Principal Investigator’s responsibility to ensure activity specific laboratory procedures and/or processes are taken into account when using this Chemical Class SOP.
This Chemical Class SOP is intended to provide general guidance on how to work safely with acutely toxic chemicals. If you have questions concerning the applicability of any item listed in this procedure, contact the Principal Investigator/Laboratory Supervisor of your laboratory or Environment, Health and Safety.
Potential Hazards
In addition, compounds with a high level of acute toxicity are defined by LD50 and LC50 levels:
- A chemical with a median lethal dose (LD50) of 50 mg or less per Kg of body weight when administered orally to albino rats weighing between 200 and 300gm each.
- A chemical with a median lethal dose (LD50) of 200 mg or less per Kg of body weight when administered by continuous skin contact for 24 hours (or less if death occurs within 24 hours) with the bare skin of albino rabbits weighing between 2 and 3 Kg each.
- A chemical that has a median lethal concentration (LC50) in air of 200 ppm by volume or less of gas or vapor, or 2 mg per liter or less of mist, fume, or dust, when administered by continuous inhalation for 1 hour (or less if death occurs within 1 hour) to albino rats weighing between 200 and 300 gm each.
Acutely toxic chemicals may also have other hazardous properties in addition to acute toxicity. Safe use requires assessing all potential hazards.
Administrative Controls
- Never work alone with extremely hazardous materials/operations. Ask the Principal Investigator for specific prohibitions (if any) on working alone with any acutely toxic chemical.
- Certain extremely hazardous operations should not be performed if the PI or Lab Safety Contact(s) are not present.
- Eliminate or substitute for a less hazardous material when possible.
- Design your experiment to use the least amount of material possible to achieve the desired result.
- Do not exceed the scale of procedures specified in Lab Specific Instructions without approval of the PI.
- Verify your experimental set-up and procedure prior to use.
- Know the location of the nearest eyewash, safety shower, and fire extinguisher before beginning work.
- Certain extremely hazardous operations should be performed in a designated area. A designated area is where limited access, special procedures, knowledge, and work skills are required. A designated area can be the entire laboratory, a specific laboratory workbench, or a laboratory hood.
- Designated areas must be clearly marked with signs that identify the chemical hazard and include an appropriate warning; for example: WARNING! ACUTELY TOXIC CHEMICAL WORK AREA!
- Upon leaving a designated area, remove any personal protective equipment worn and wash hands, forearms, face, and neck.
- Decontamination procedures vary depending on the material being handled. The toxicity of some materials can be neutralized with other reagents.
- All surfaces should be wiped with the appropriate cleaning agent following dispensing or handling.
- Decontaminate vacuum pumps or other contaminated equipment (glassware) before removing them from the designated area.
- At the end of each project, thoroughly decontaminate the designated area before performing other laboratory work in the area.
- Waste materials generated should be treated as a hazardous waste.
Engineering Controls
- Use a properly functioning certified chemical fume hood when handling this material. If the process does not permit the handing of such materials in a fume hood, contact Environment, Health and Safety for reviewing the adequacy of ventilation measures.
- Use containment devices (such as lab fume hoods or glove boxes) when: (i) volatilizing these substances, (ii) manipulating substances that may generate aerosols, and (iii) performing laboratory procedures that may result in uncontrolled release of the substance.
- Use high efficiency particulate air (HEPA) filters, carbon filters, or scrubber systems with containment devices to protect effluent and vacuum lines, pumps, and the environment whenever feasible. There must be regularly scheduled inspection of such filters to insure their continued effectiveness.
- Use ventilated containment to weigh out solid chemicals. Alternatively, the tare method can be used to prevent inhalation of the chemical. While working in a laboratory hood, the chemical is added to a pre-weighed container. The container is then sealed and can be re-weighed outside of the hood. If chemical needs to be added or removed, this manipulation is carried out in the hood. In this manner, all open chemical handling is conducted in the laboratory hood.
Personal Protective Equipment (PPE)
NOTE: Lab-specific information on PPE selection may be included in Lab Specific Instructions.
Respiratory protection
NOTE: Lab personnel intending to use/wear a respirator mask must be trained and fit-tested by EH&S. This is a regulatory requirement.
Refer to WAC 296-62 for selection of respirators. A respiratory protection program that meets WAC 296- 62 must be followed whenever workplace conditions warrant use of a respirator.
Respirators should be used only under any of the following circumstances:
- As a last line of defense (i.e., after engineering and administrative controls have been exhausted).
- When Permissible Exposure Limit (PEL) has exceeded or when there is a possibility that PEL will be exceeded.
- Regulations require the use of a respirator.
- An employer requires the use of a respirator.
- There is potential for harmful exposure due to an atmospheric contaminant (in the absence of PEL)
- As PPE in the event of a chemical spill clean-up process
Hand Protection
Handle with gloves. Gloves must be inspected prior to use. Use proper glove removal technique (without touching glove's outer surface) to avoid skin contact with this product. Dispose of contaminated gloves after use in accordance with applicable laws and good laboratory practices. Wash and dry hands.
Eye Protection
Safety glasses with side shields or tightly fitting safety goggles. Use face shield (8-inch minimum) when appropriate. Use equipment for eye protection tested and approved under appropriate government standards such as NIOSH (US) or EN 166(EU) or ANSI Z87.1.
Skin and Body Protection
Long pants, closed-toed and closed-heeled shoes, cotton-based clothing/attire, and flame resistant (where appropriate) lab coat must be worn for protecting against chemical hazards.
Additional PPE may be required if procedures or processes present additional risk. It is the responsibility of the PI to ensure that any additional PPE requirements are identified and communicated to research staff.
Storage
Use unbreakable secondary containment for the storage of acutely toxic chemicals. If the materials are volatile (or could react with moisture or air to form volatile toxic compounds), containers should be in a ventilated storage area. All containers of acutely toxic chemicals should be clearly labeled with chemical composition, known hazards, and warnings for handling.
Chemicals that can combine to make toxic materials (e.g., acids and inorganic cyanides, which can generate hydrogen cyanide) should not be stored in the same secondary containment. Chemicals that have a limited shelf life need to be tracked and monitored. Chemicals that require refrigeration should be stored appropriately.
Dispose of Waste
- Dispose of regularly generated chemical waste within six (6) months.
- Call EH&S for questions
Spill Response and Exposure Response
Before beginning work with chemicals, review the relevant SOPs, Safety Data Sheets, and other chemical safety resources. Develop specific procedures for emergency response and chemical exposure or injury to staff, including any special first aid measures required for the relevant chemicals.
Spill and Accident Procedure
Note: These responses may not apply to all acutely toxic chemicals. Please review specific chemical SOPs and SDSs for specific response to spills and accidents. Always dial 911 for assistance.
Chemical Spill Dial 911
Spill – Assess the extent of danger. Help contaminated or injured persons. Evacuate the spill area. Avoid breathing vapors. If possible, confine the spill to a small area using a spill kit or absorbent material. Keep others from entering contaminated area (e.g., use caution tape, barriers, etc.). Dial 911 for assistance.
Chemical Spill on Body or Clothes – Remove clothing and rinse body thoroughly in emergency shower for at least 15 minutes. Seek medical attention. Notify supervisor and EH&S immediately. Follow up with a call to EH&S at 506-963-2338 to report the incident.
Chemical Splash Into Eyes – Immediately rinse eyeballs and inner surfaces of eyelids with water from the emergency eyewash station for 15 minutes by forcibly holding the eye open. Seek medical attention. Notify supervisor and EH&S immediately. Follow up with a call to EH&S at 509-963-2338 to report the incident.
Medical Emergency Dial 911
Life Threatening Emergency, After Hours, Weekends and Holidays – Dial 911 or go to the nearest emergency room. Note: All serious injuries must be reported to EH&S within 8 hours. Follow up with a call to 509-963-2338 to report the incident.
Non-Life Threatening Emergency – If student, have them go to the Student Health Clinic on campus. If staff or faculty, go to the KVH. After hours go to the nearest emergency room. Note: All serious injuries must be reported to EH&S within 8 hours. Follow up with a call to 509-963-2338 to report the incident.
Needle stick/puncture exposure (as applicable to chemical handling procedure) – Wash the affected area with antiseptic soap and warm water for 15 minutes. For mucous membrane exposure, flush the affected area for 15 minutes using an eyewash station. If student, have them go to the Student Health Clinic on campus. If staff or faculty, go to the KVH. After hours go to the nearest emergency room. Note: All needle stick/puncture exposures >must be reported to EH&S within 8 hours. Follow up with a call to 509-963-2338 to report the incident.
Training of Personnel
- Prior to conducting any work with Acutely Toxic Chemicals, designated personnel must provide training to his/her laboratory personnel specific to the hazards involved in working with the specific chemical(s) used, work area decontamination, and emergency procedures.
- The Principal Investigator must provide his/her laboratory personnel with a copy of this SOP and a copy of the SDS provided by the manufacturer.
-
Alkali Metals SOP
Principal Investigator (PI) Approval is Required Prior to Performing this Procedure
Description
The handling and usage of alkali metals, specifically lithium, sodium, and potassium.
Potential Hazards
Alkali metals react very vigorously with water resulting in the formation of hydrogen gas. This gas can then spontaneously ignite, causing fires. Additionally, if inhaled, the dust of alkali-metal oxides can cause damage to the mucous membranes and upper respiratory tracts. Contact of any of these metals with the skin or eyes may results in burns. Caustic oxides are formed as the metals burn.
Of these three, potassium and the liquid alloy of potassium and sodium are the most reactive, while lithium is the least reactive.
Engineering Controls
Ensure adequate ventilation.
Work Practice Controls
Use of lithium, sodium, or potassium metal requires proper training and demonstration of correct technique by an appropriate lab member. The MSDS sheets should also be consulted before first use.
These metals must not be used when working alone.
Lithium, sodium, and potassium metals should only be used in a dry environment away from sparks or any source of ignition. Good ventilation and access to a dry chemical or dry powder fire extinguisher are also necessary. The area where the metals will be handled should be free of other chemicals and flammable objects.
Personal Protective Equipment (PPE)
- Respiratory Protection
- Where risk assessment shows air-purifying respirators are appropriate use a full-face particle respirator type N100 (US) respirator cartridges as a backup to engineering controls. Use respirators and components tested and approved under appropriate government standards such as NIOSH (US).
- Hand Protection
- Handle with gloves.
- Eye Protection
- Safety glasses.
- Skin and Body Protection
- A flame-retardant lab coat must be worn while handling these compounds.
- Hygiene Measures
- Handle in accordance with good industrial hygiene and safety practice. Wash hands before breaks and at the end of workday.
Storage Requirements
- Store in a dry, cool place away from any source of ignition. Store under paraffin oil, mineral oil, or kerosene. When cutting or weighing out sodium or potassium, they must be kept under hexanes or toluene as much as possible to prevented them from reaction with the moisture in the air.
- The container holding the metal must be kept closed, and the amount of material exposed to the air kept to a minimum. N2 is not an inert gas for lithium, as lithium nitride is formed and can also react violently with water. Lithium should therefore not be kept under nitrogen for a prolonged period of time (use Ar instead).
Decontamination
All materials – disposable gloves, wipers, bench paper, etc. - that are contaminated with pyrophoric chemicals should be disposed as hazardous waste (after appropriate quenching of the compound, see section 10 of Safety Data Sheet).
Spill Procedures
- EHS&S (509-963-2252) and Campus Safety should be called in the event of a large spill or fire: (Emergencies: 911; Non-emergencies 509-925-8534)
- DO NOT use water to attempt to extinguish a reactive material fire as it can actually enhance the combustion.
- Do not use combustible materials (paper towels) to clean up a spill, as these may increase the risk of igniting the reactive compound. Soda ash (powdered lime) or dry sand should be used to completely smother and cover any small spill that occurs.
- A container of soda ash (powdered lime) or dry sand should be kept within arm’s length when working with a reactive material.
- If anyone is exposed, or on fire, smothering the fire is a better course of action than washing with water because water can fuel the fire.
- Class D extinguishers are recommended for combustible solid metal fires.
- Call 9-1-1 for emergency assistance and for assistance with all fires, even if extinguished.
Waste Disposal
After completion of the cutting process, the weigh boat or other weighing container should be rinsed carefully with a solvent which will react with the excess metal much more slowly than with water (i.e. methanol, isopropanol).
- Disposal of Pyrophoric Reagents
- Any container with a residue of reactive materials should never be left open to the atmosphere.
- Any unused or unwanted reactive materials must be destroyed by transferring the materials to an appropriate reaction flask for hydrolysis and/or neutralization with adequate cooling.
Training of Personnel
All personnel are required to complete the Chemical Hygiene Plan training. Furthermore, all personnel shall read and fully adhere to this SOP when handling the chemical.
- Respiratory Protection
-
Carcinogen SOP
Principal Investigator (PI) Approval is Required Prior to Performing this Procedure
Description
Standard operating procedures (SOP) are intended to provide you with general guidance on how to safely work with a specific class of chemical or hazard. This SOP is generic in nature. It addresses the use and handling of substances by hazard class only. In some instances multiple SOPs may be applicable for a specific chemical (i.e., both the SOPs for flammable liquids and carcinogens would apply to benzene). If you have questions concerning the applicability of any items listed in this procedure contact Environmental Health & Safety 509-963-2338 or the Principal Investigator of your laboratory. Specific written procedures are the responsibility of the principal investigator.
If compliance with all the requirements of this standard operating procedure is not possible, the principal investigator must develop a written procedure that will be used in its place. This alternate procedure must provide the same level of protection as the SOP it replaces.
A carcinogen commonly describes any agent that can initiate or speed the development of malignant or potentially malignant tumors, malignant neoplastic proliferation of cells, or cells that possess such material.
Potential Hazards
- Hazard assessment should focus on proper use and handling techniques, education of laboratory workers concerning the health risks posed by carcinogens, and the demarcation of designated areas.
- You should notify Environmental Health Safety 509-963-2338 prior to the initial use of carcinogens. Notification is also required following significant changes in procedures or the quantity of materials used.
Engineering Controls
- Fume Hood
- Manipulation of carcinogens should be carried out in a fume hood. If the use of a fume hood proves impractical refer to the section on special ventilation.
- All areas where carcinogens are stored or manipulated must be labeled as a designated area.
- Glove (Dry) Box
- Certain carcinogens must be handled in a glove box rather than a fume hood. Environmental Health & Safety 509-963-2252 or the Principal Investigator will determine if this is required.
- Special Ventilation
- Manipulation of carcinogens outside of a fume hood may require special ventilation controls in order to minimize exposure to the material. Fume hoods provide the best protection against exposure to carcinogens in the laboratory and are the preferred ventilation control device. When possible, handle carcinogens in a fume hood. If the use of a fume hood proves impractical, attempt to work in a glove box or on an isolated area on the bench top.
- If available, consider using a Biological Safety Cabinet. The biological safety cabinet is designed to remove particulates (the carcinogen) before the air is discharged into the environment. Carcinogens that are volatile must not be used in a biological safety cabinet unless the cabinet is vented to the outdoors.
- If your research does not permit the handling of carcinogens in a fume hood, biological safety cabinet, or glove box, you must contact the Environmental Health & Safety 509-963-2252.
- All areas where carcinogens are stored or manipulated must be labeled as a designated area.
- Personal Protective Equipment (PPE)
-
- Eye protection in the form of safety glasses must be worn at all times when handling carcinogens. Ordinary (street) prescription glasses do not provide adequate protection. (Contrary to popular opinion these glasses cannot pass the rigorous test for industrial safety glasses.) Adequate safety glasses must meet the requirements of the Practice for Occupational and Educational Eye and Face Protection (ANSI Z.87. 1 1989) and must be equipped with side shields. Safety glasses with side shields do not provide adequate protection from splashes; therefore, when the potential for splash hazard exists other eye protection and/or face protection must be worn.
- Eyewash
- Where the eyes or body of any person may be exposed to carcinogens, suitable facilities for quick drenching or flushing of the eyes and body shall be provided within the work area for immediate emergency use. Bottle type eyewash stations are not acceptable.
- Protective Apparel
- Lab coats, closed toed shoes and long sleeved clothing should be worn when handling carcinogens. Additional protective clothing should be worn if the possibility of skin contact is likely.
- Gloves
- Gloves should be worn when handling carcinogens. Disposable nitrile gloves provide adequate protection against accidental hand contact with small quantities of most laboratory chemicals. Lab workers should contact EH&S for advice on chemical resistant glove selection when direct or prolonged contact with hazardous chemicals is anticipated.
- Safety Shower
- A safety or drench shower should be available in a nearby location where the carcinogens are used.
- Safety Shielding
- Safety shielding is required any time there is a risk of explosion, splash hazard or a highly exothermic reaction. All manipulations of carcinogens which pose this risk should occur in a fume hood with the sash in the lowest feasible position. Portable shields, which provide protection to all laboratory occupants, are acceptable.
- Vacuum Protection
- Evacuated glassware can implode and eject flying glass, and splattered chemicals. Vacuum work involving carcinogens must be conducted in a fume hood, glove box or isolated in an acceptable manner.
- Mechanical vacuum pumps must be protected using cold traps and, where appropriate, filtered to prevent particulate release. The exhaust for the pumps must be vented into an exhaust hood.
- Signs and Labels
- Doorways: The room sign must contain a Designated Area Within Caution where carcinogens, reproductive hazards, and/or acutely toxic chemicals are stored or used.
- Containers: All containers of carcinogens must be clearly labeled with the correct chemical name. Handwritten labels are acceptable; chemical formulas and structural formulas are not acceptable.
-
- Special Storage
- Carcinogens must be stored in a designated area.
- Designated Area
- The room sign for the laboratory must contain a Designated Area Within identifier.
- All locations within the laboratory where carcinogens are handled should be demarcated with designated area caution tape and/or posted with designated area caution signs. This includes all fume hoods and bench tops where the carcinogens are handled.
- Where feasible, carcinogens should be manipulated over plastic-backed disposable paper work surfaces. These disposable work surfaces minimize work area contamination and simplify clean up.
- Waste Disposal
- All materials contaminated with carcinogens should be disposed of as hazardous waste. Wherever possible, attempt to design research in a manner that reduces the quantity of waste generated. Questions regarding waste pick up should be directed to Environmental Health & Safety 509-963-2338. Waste must be disposed of following your laboratory-specific chemical hygiene plan and the requirements of Central Washington University’s Chemical Waste Policy and the Laboratory Chemical Waste Management Practices.
- Decontamination Procedures
- Personnel: Wash hands and arms with soap and water immediately after handling carcinogens.
- Area: Decontamination procedures vary depending on the material being handled. The toxicity of some materials can be neutralized with other reagents. All surfaces should be wiped with the appropriate cleaning agent following dispensing or handling. Waste materials generated should be treated as a hazardous waste.
- Equipment: Decontaminate vacuum pumps or other contaminated equipment (glassware) before removing them from the designated area.
- Spill Response
- Anticipate spills by having the appropriate clean up equipment on hand. The appropriate clean up supplies can be determined by consulting the material safety data sheet. This should occur prior to the use of any carcinogen.
- In the event of a spill, alert personnel in the area that a spill has occurred. Do not attempt to handle a large spill of carcinogenic material. Vacate the laboratory immediately and call for assistance.
- Environmental Health Safety 509-963-2255 or 963-2252
- Central Washington University Public Safety Emergency Number 911 from a campus phone.
- Remain on the scene, but at a safe distance, to receive and direct safety personnel when they arrive.
- Emergency Procedure
- Emergency procedures which address response actions to fires, explosions, spills, injury to staff, or the development of sign and symptom of overexposure must be developed. The procedures should address as a minimum the following:
- Who to contact:
- (University Police, Environmental Health & Safety 509-963-2252, and Principal investigator of the laboratory including evening phone number)
- The location of all safety equipment (showers, eye wash, fire extinguishers, etc.)
- The method used to alert personnel in nearby areas of potential hazards
- Special first aid treatment required by the type of carcinogens handled in the laboratory
- Who to contact:
- Emergency procedures which address response actions to fires, explosions, spills, injury to staff, or the development of sign and symptom of overexposure must be developed. The procedures should address as a minimum the following:
- Training of Personnel
- All personnel are required to complete the Chemical Hygiene Plan training. Furthermore, all personnel shall read and fully adhere to this SOP when handling the chemical.
-
Compressed Gas SOP
Description
Standard operating procedures (SOP) are intended to provide you with general guidance on how to safely work with a specific class of chemical or hazard. This SOP is generic in nature. It addresses the use and handling of substances by hazard class only. In some instances, multiple SOPs may be applicable for a specific chemical (i.e., both the SOPs for flammable liquids and carcinogens would apply to benzene). If you have questions concerning the applicability of any item listed in this procedure contact Environmental Health & Safety Department (509) 963-2352 or the Principal Investigator of your laboratory. Specific written procedures are the responsibility of the principal investigator.
If compliance with all the requirements of this standard operating procedure is not possible, the principal investigator must develop a written procedure that will be used in its place. This alternate procedure must provide the same level of protection as the SOP it replaces. The Office of Environmental Health and Safety is available to provide guidance during the development of alternate procedures.
Additional requirements may apply if the materials are acutely toxic compressed gas. Please refer to the SOP for acutely toxic gases if applicable.
Securing of Gas Cylinders
Cylinders of compressed gases must be handled as high energy sources. They pose a serious hazard if the cylinder valve is dislodged. When storing or moving a cylinder, have the cap securely in place to protect the stem. Use suitable racks, straps, chains or stands to support cylinders. Do not store cylinders or lecture bottles with the regulator in place. If the regulator fails, the entire contents of the gas cylinder may be discharged.
Designated Area
Compressed gas cylinders which contain acutely toxic gases must be stored in a designated area. See the SOP for acutely toxic compressed gases.
Emergency Procedure
Emergency procedures that address response actions to fires, explosions, spills, injury to staff, or the development of signs and symptoms of overexposure must be developed. The procedures should address as a minimum the following:
Who to contact: (University police, and Office of Environmental Health and Safety, Principal investigator of the laboratory including evening phone number)
- The location of all safety equipment (showers, eye wash, fire extinguishers, etc.)
- The method used to alert personnel in nearby areas of potential hazards
- Special first aid treatment required by the type of compressed gas handled in the laboratory
Personal Protective Equipment (PPE)
- Eye Protection
- Eye protection in the form of safety glasses must be worn at all times when handling compressed gases. Ordinary (street) prescription glasses do not provide adequate protection. (Contrary to popular opinion these glasses cannot pass the rigorous test for industrial safety glasses.) Adequate safety glasses must meet the requirements of the Practice for Occupational and Educational Eye and Face Protection (ANSI Z.87. 1 1989) and must be equipped with side shields.
- Eyewash
- Not applicable.
- Fume hood
- Manipulation of compressed gases should typically be carried out in a fume hood if the compressed gas is an irritant, oxidizer, asphyxiate, or has other hazardous properties.
- Glove (dry) box
- Not applicable
- Gloves
- Not applicable
- Hazard assessment
- Hazard assessment for work with compressed gases should assure that all staff understands proper use and handling precautions; that all pressurized equipment is properly shielded; regulators are not interchanged between different gas types; all hose connections are properly secured and are appropriate for the pressure(s) used.
- Protective Apparel
- Lab coats, closed-toed shoes, and long-sleeved clothing should be worn when handling compressed gases.
- Safety shielding
- Safety shielding is required any time there is a risk of explosion, splash hazard, or a highly exothermic reaction. All manipulations of compressed gases which pose this risk should occur in a fume hood with the sash in the lowest feasible position. Portable shields, which provide protection to all laboratory occupants, are acceptable.
- Safety shower
- Not applicable
- Signs and labels
- Containers: All compressed gases must be clearly labeled with the correct chemical name. Handwritten labels are acceptable; chemical formulas and structural formulas are not acceptable. The compressed gas cylinder should be labeled to indicate if the container is full or empty.
Special Ventilation
Manipulation of compressed gas that is an irritant, oxidizer, asphyxiate, or has other hazardous properties outside of a fume hood may require special ventilation controls in order to minimize exposure to the material. Fume hoods provide the best protection against exposure to compressed gases in the laboratory and are the preferred ventilation control device. If you have questions contact the Office of Environmental Health and Safety to review the adequacy of all special ventilation.
Transportation and Storage
Cylinders should be stored in an upright position and secured to a wall or laboratory bench through the use of chains or straps. Cylinder caps should remain on the cylinder at all times unless a regulator is in place. Cylinders should be stored in areas where they will not become overheated. Avoid storage near radiators, areas in direct sunlight, steam pipes, and heat-releasing equipment such as sterilizers.
Transport compressed gas cylinders on equipment designed for this function. Never carry or "walk" cylinders by hand.
Waste Disposal
All empty or partially filled compressed gas cylinders should be returned to the supplier. If the supplier does not accept empty or partially filled cylinders, contact the Office of Environmental Health and Safety concerning disposal.
Spill response
In the event of a spill of a compressed gas that is an irritant, oxidizer, asphyxiate, or has other hazardous properties all personnel in the area should be alerted. Vacate the laboratory immediately and call for assistance.
- Office of Environmental Health & Safety, (509) 963-2352
- University Police 911 from a campus phone. This is a 24-hour service. Remain on the scene, but at a safe distance, to receive and direct safety personnel when they arrive.
Training of Personnel
All personnel are required to complete the Chemical Hygiene Plan training. Furthermore, all personnel shall read and fully adhere to this SOP when handling the compressed gas cylinder.
-
Compressed Gas Cylinders, Pressurized Equipment, and Pressure Vessels
Definition
A compressed gas is defined as any single gas or mixture of gases in a container with a pressure exceeding 40 psi at 70°F/21°C, 104 psi at 130°F/55°C, or any flammable liquid with an absolute vapor pressure exceeding 40 psi at 100°F/38°C.
Hazards
Cylinders of compressed gases can pose a chemical hazard as well as a physical hazard. If the valve were to break off a cylinder, the amount of force present could propel the cylinder through a brick wall. For example, a cylinder of compressed breathing air used by SCUBA divers has an explosive force of 1 ½ pounds of TNT.
Container Requirements for Compressed Gases
- All compressed gas cylinders or containers delivered to or shipped from the University must be marked, labeled, stored, and handled in accordance with all applicable rules and regulations, including DOT, OSHA, and NFPA standards.
- The contents of each cylinder and container must be clearly identified by tag or stamp on the cylinder.
- University faculty, staff, and students must not remove or alter any identification on a compressed gas cylinder.
- Do not purchase a larger cylinder size than necessary. Only gases in returnable containers should be selected for purchase—lecture bottles are an exception.
Storage of Compressed Gas Cylinders
- Storage areas for compressed gas cylinders must be designed to accommodate the gases used and provide adequate spacing and/or segregation in accordance with applicable building codes and regulations. Compressed gas cylinder storage areas must be segregated from exit corridors and egress paths.
- Storage areas should be designated by hazard class and marked clearly with appropriate warning signs that restrict access.
- Consideration must be given to separate storage of full and empty containers. Incompatible gases must be separated by at least 20 feet or separated by using appropriate fire-rated barriers.
- The cylinder storage area should be dry, free of combustible materials and debris (e.g. timber, cardboard, packaging materials) to prevent flame impingement on gas cylinders in a fire, well-ventilated, and be of fire-resistant construction when necessitated by the gas in storage.
- Compressed gas cylinders must not be stored near sources of heat and ignition or near corrosive chemicals or fumes.
- Compressed gas cylinders must not be stored near unprotected platform edges or in any location where heavy moving objects may strike or fall on them.
- All compressed gas cylinders (whether empty or full) must be secured in an upright position using an approved chain, strap, or floor device to prevent falling. There should be no more than five cylinders per securing device. When small-size cylinders are in use, they shall be attached to a cylinder stand or an apparatus of sufficient size to render the entire assembly stable.
- Approved chains or straps should be secured around the top 1/3 and 2/3 of the cylinder. Securing devices should never be around the neck or regulator.
- All compressed gas cylinders must be fitted with a protective valve cap or guard while in storage.
- If the use of small non-refillable cylinders (lecture bottles) is unavoidable, they should be secured in a device, cage, or box designed for cylinders 18 inches or smaller.
- Toxic gases (such as F2, CO, and H2S) should be stored and used in a chemical fume hood. If this is not feasible, the area of use must be equipped with a detection system specific to the toxic gas or inhalation hazard.
- Oxygen should be stored in an area that is at least 20 feet away from any flammable or combustible materials, or separated from them by a noncombustible barrier at least 5 feet high and having a fire-resistance rating of at least 1/2 hour.
- Position all cylinders so that the main valve is always accessible.
Safe Handling of Compressed Gas Cylinders
- Persons handling compressed gas cylinders must:
- Be familiar with the hazards of compressed gas.
- Always use a cylinder cart or other transport device to move cylinders in a secure fashion. Never drag a cylinder by valves or caps or roll a cylinder in a horizontal position. Compressed gas cylinders should be transported with the cylinder cap securely fastened.
- Never use a compressed gas cylinder as a support or door stop.
- Keep caps on cylinders unless connected to dispensing equipment systems.
- Never expose cylinders to temperature extremes, direct flame, or heat.
- Never use a gas cylinder that cannot be positively identified. Color coding is not a reliable way of identifying a gas cylinder because the colors can vary from supplier to supplier.
- Empty compressed gas cylinders must be:
- Closed
- Secured at all times
- Labeled to indicate “empty”
- Regulators control the rate at which gas is delivered from the cylinder so the gas may be used safely. Never discharge a gas without the use of a regulator. Compressed gas piping, regulators, and flow control equipment must be:
- Compatible with the chemical and physical properties of gas.
- Capable of withstanding gas supply pressures.
- Installed and operated by trained and qualified persons familiar with the specific hazards of the gases in use.
- Grounded to minimize sparks due to static discharge when using flammable gas.
- Provided with a means for safely purging the system and devices to prevent backflow of gases or liquids into the gas storage cylinders when using hygroscopic corrosive gases, such as anhydrous HCl.
- Always use the appropriate regulator on a cylinder.
- If a regulator will not fit a cylinder's valve, replace the cylinder, not the regulator.
- Do not ever attempt to adapt or modify a regulator to fit a cylinder for which it was not designed. Regulators are designed to fit only specific cylinder valves to avoid improper use.
- Inspect regulators, pressure relief devices, valves, cylinder connections, and hose lines frequently for damage.
- Do not use oil or grease on any cylinder component of an oxidizing gas because a fire or explosion can result.
- Never transfer gases from one cylinder to another.
- The gas may be incompatible with the residual gas remaining in the other cylinder.
- The gas may be incompatible with the material of which the cylinder is made.
- Never completely empty cylinders.
- Leave approximately 25 psi of pressure.
- This will prevent any residual gas in the cylinder from becoming contaminated.
Emergency Procedures for Compressed Gas Cylinders
- Personnel should be aware of common emergency situations involving compressed gases and their associated hazards, such as:
- An unsecured cylinder may tip and become damaged in a manner that the release of internal pressure can cause the cylinder to become a dangerous high-speed projectile.
- A fire threatening the cylinder can cause a rupture or explosion.
- A flammable gas leak can cause a buildup of explosive gases.
- A leak can cause high concentrations of gas that exceed safe breathing levels or an inert gas leak can cause an oxygen-deficient atmosphere that is a threat to life safety.
- An unplanned chemical reaction may cause a cylinder rupture or explosion of apparatus.
- Fires involving compressed gas cylinders should be handled with extreme caution.
- Do not take unnecessary risks to save equipment—evacuate the area.
- Only when safe to do so, release pressure in affected pipelines and shut off equipment prior to evacuation.
- If safe to do so, shut off the gas supply to ignited flammable gas leaks or allow the fire to burn out while controlling the ignition of surrounding materials.
- Never attempt to extinguish a flammable gas leak without stopping the flow of gas.
- Any compressed gas cylinder involved in a fire must be taken out of service and returned to the supplier.
- Some common leak points and their potential repairs:
- Valve outlet /regulator connection: dirt in connection, damaged connector or washer.
- Valve stem spindle: tighten the adjustable gland nut ¼ turn with the valve stem loosened or tighten the lock nut if present on gland fitting.
- Cylinder valve to cylinder joint: cannot be repaired in the field, remove from service. Label and return to supplier.
- Valve closure: tighten the valve or if defective, set it aside, label and return it to the supplier.
- Leaking gas control equipment/pipelines: isolate gas supply, release pressure, and purge equipment of hazardous gas before attempting the repair.
- Use only wrenches or other tools supplied by the cylinder manufacturer to open a valve.
- Open cylinder valves slowly.
Disposal of Compressed Gas Cylinders
- Contact your cylinder vendor to return damaged, excess, or unknown cylinders. All users will be responsible for returning all cylinders to the manufacturer/distributor.
- Cylinders of gases classified as corrosive or highly reactive shall be returned to the manufacturer/distributor within one year of the purchase date and all other gases within three years.
Pressurized Equipment and Pressure Vessels
Common examples of pressure vessels or pressurized equipment are steam boilers, autoclaves, compressor tanks, pressurized research equipment, reactors, and calorimeters. University employees should follow these basic safety guidelines when working with pressure vessels or pressurized equipment:
- Pressurized equipment used at pressures at or above 103 kPa gauge (15 psi) must be designed and constructed by qualified individuals for use at the expected temperature, pressure, and other operating conditions.
- Pressure equipment must be fitted with a pressure relief device, such as a ruptured disc, relief valve, or blow-down valve. This pressure relief device must be vented to a safe location.
- Laboratory pressure vessels or equipment operated at pressures above 103 kPa gauge (15 psi) must be operated and maintained according to the manufacturer’s instructions, the design limitations of the equipment, and applicable codes and regulations.
- This equipment must be inspected at least annually.
- Any significant change in the condition of the equipment, such as corrosion, cracks, distortion, scale formation, chemical attack, weakening of the closure, or the inability of the equipment to maintain pressure, should be documented.
- Equipment exhibiting any of the above changes must be removed from service immediately and shall not be returned to service until repaired and approved by a qualified person.
References:
-
Cryogenic Liquids Safety
Description
This standard is to provide guidelines for the safe handling of cryogenic liquids. A cryogenic liquid is a liquid that has a boiling point at or below -150 0C. Consult the M/SDS for specific information about a particular cryogen liquid before working with it.
Potential Hazards
-
- Fire. The use of cryogenic liquids such as nitrogen, argon, helium, or hydrogen will condense oxygen from the atmosphere. Exposure of combustible materials to oxygen-enriched cryogenic liquids enhances the combustibility of the material.
- Explosion. A cryogenic liquid expands by orders of magnitude upon vaporization. For example, one liter of liquid nitrogen becomes 24.6 cubic feet of nitrogen gas. This can cause an explosion of a sealed container.
- Asphyxiation. A poorly or non-ventilated room will be quickly enveloped by the expanding gas from a cryogenic liquid. This will lead to the displacement of oxygen and potential asphyxiation of the user.
- Contact. Cryogenic liquids cause frostbite on contact with exposed skin.
Process or Experiment Description
This standard operating procedure (SOP) is intended to provide general guidance on how to safely work with cryogenic liquids and dry ice. This general-use SOP only addresses safety issues specific to cryogenic hazards of chemicals. In some instances, several general-use SOPs may be applicable for a specific chemical (i.e., for liquid hydrogen, both this general-use SOP and the general-use SOP for flammable liquids would apply). If you have questions concerning the applicability of any item listed in this procedure contact Environmental Health and Safety (509) 963-2252.
Hazardous Chemicals/Class of Hazardous Chemicals
Cryogenic liquids are materials with extremely low boiling points (i.e. less than – 150 °C). Common examples of cryogenic liquids are liquid nitrogen, helium, and argon. Dry ice is the common term for frozen carbon dioxide. One special property of both cryogenic liquids and dry ice is that they undergo substantial volume expansion when converted to a gas phase, which can potentially lead to an oxygen-deficient atmosphere where ventilation is limited. Few cryogenic liquids can also pose additional hazards including toxicity and flammability (i.e. liquid carbon monoxide).
Control of Hazards – General
- Only work with cryogenic liquids in well-ventilated areas to avoid localized oxygen depletion or buildup of flammable or toxic gas.
- Handle objects that are in contact with cryogenic liquids with tongs or proper gloves.
- Transfers or pouring of cryogenic liquids should be done carefully to avoid splashing.
- Containers and systems containing cryogenic liquids should have pressure relief mechanisms.
- Cryogenic liquid cylinders and other containers (such as Dewar flasks) should be filled at no more than 80% of capacity to protect against thermal expansion.
- Cryogenic liquid/dry ice baths should be open to the atmosphere to avoid pressure build-up.
- Keep liquid oxygen away from organic materials and ignition sources.
- Transfer of liquid hydrogen in an air atmosphere can condense oxygen in the liquid hydrogen, creating an explosion risk.
- Cryotube thawing - In addition to wearing proper safety equipment, when thawing cryotubes, place the cryotube in a heavy-walled container (e.g., a desiccator) or behind a safety shield to protect yourself in the event that the tube shatters.
- Shield or wrap fiber tape around glass Dewars to minimize flying glass and fragments should an explosion occur. Note: Plastic mesh will not stop small glass fragments.
Engineering/Ventilation Controls
If the process does not permit the handling of cryogenic liquids in well-ventilated areas (i.e., lab ventilation having a minimum of 6 air changes per hour).
Personal Protective Equipment
At a minimum, chemical splash goggles, long pants, and closed-toed shoes are to be worn when entering laboratories having hazardous chemicals. Additionally, when handling cryogenic liquids, heavy gloves (e.g., cryogenic gloves) are appropriate.
Special Handling Procedures
- Never allow any unprotected part of the body to touch exposed pipes/vessels containing cryogenic liquids; skin coming in contact with the cold metal may adhere to it and tear when attempting to withdraw.
- Exercise caution when adding a cryogenic liquid to a Dewar at room temperature or an object at room temperature to a cryogenic liquid. Both will cause the liquid to boil and splash vigorously.
- Keep ignition sources away when handling cryogenic liquids, especially liquid oxygen. Combustible materials (including the user) may become oxygen-enriched or saturated through exposure and, in the presence of an ignition source, will ignite rapidly and burn fiercely.
- Only use containers or equipment specified for cryogenic use.
- Never plug containers holding cryogenic liquid; cover them when not in use to prevent an accumulation of moisture and ice.
- Inspect pressure relief valves on equipment (e.g. 150-L Dewar) for ice build-up.
Storage Requirements
- Cryogenic liquid Dewars are to be stored in well-ventilated areas. Storage in unventilated closets, environmental rooms, and stairwells is prohibited.
- Large Dewar must be tethered/ anchored to a wall.
- Store flammable cryogenic liquids and liquid oxygen away from combustible materials and sources of ignition.
- Additionally, follow all substance-specific storage guidance provided in M/SDS documentation.
Spill and Accident Procedures
In the event of a small spill, evacuation may not be necessary if the area is well-ventilated. Small spills will evaporate in time. In the event of a large chemical spill, follow these guidelines:
- Notify everyone in the immediate area and the supervisor.
- Evacuate personnel from the spill area.
- Deny entry.
- Alert other building occupants. NOTE: Evacuation of the building and its occupants may be necessary depending on the volume of cryogen spilled and its relative hazard.
- Call 911
Labeling Requirements
Identify containers with the name of the cryogenic liquid e.g. liquid nitrogen. Label storage areas appropriately as well.
Dewar Disposal
Coordinate w/ vendor for return of Dewar(s).
Minimum Training Requirements
- Laboratory-specific training
First Aid and Decontamination Procedures
Unprotected skin contact with cryogenic liquids will cause frostbite. Contact 911 and request medical assistance.
Personnel: If skin or eye(s) comes in contact with a cryogenic liquid, run the area of skin under cool or warm water for fifteen minutes (do not use hot or cold water). DO NOT RUB OR MASSAGE AFFECTED AREAS— this can cause further tissue damage. Refer to M/SDS for any specific instructions. Where medical attention is required, ensure to bring along M/SDS(s) of chemical(s) to aid medical staff in proper diagnosis and treatment.
Designated Area
For cryogens that are also considered particularly hazardous substances, a designated area shall be established per the other applicable SOP(s).
-
-
Ethidium Bromide SOP
Principal Investigator (PI) Approval is Required Prior to Performing this Procedure
- Description
- Ethidium bromide is used in staining DNA; visualization of nucleic acids.
- Hazards
- Potent mutagen; moderately toxic
- Ethidium bromide (CAS Registry Number 1239-45-8).
- The material fluoresces a red-orange color under ultraviolet light, with increased fluorescence when the material is bound to double-stranded DNA. Ethidium bromide is typically purchased in powder or solution form and is soluble in water. The crystal or powder form is odorless and appears dark red in color.
- The powder form is considered an irritant to the upper respiratory tract, eyes, and skin. Ethidium bromide is strongly mutagenic, causing living cell mutations. Even though there is no evidence at this time of human carcinogenicity or teratogenicity, this material should be considered a possible carcinogen or teratogen.
- SybrSafe is a safer alternative to ethidium bromide. While it should be handled and disposed of as ethidium bromide, it is somewhat less mutagenic and therefore safer to handle.
- Particularly Hazardous Substance Involved?
- Yes - 9 AND 11 are Mandatory
- No - 9 AND 11 are Optional
- Personal Protective Equipment (PPE)
- Lab coat, chemical splash goggles and nitrile gloves are required. Leave lab coats in the lab when your work is complete to prevent the spread of this or other chemicals outside of the lab.
- When an ultraviolet light source is used in your work with ethidium bromide, added caution is required. As a general rule, avoid exposing unprotected skin and eyes to intense UV sources. If the UV light is aimed upwards, wear a UV protective face shield when you are standing near the source. For prolonged work close to UV light boxes or other intense sources, it may be useful to wrap the end of the lab coat sleeves loosely with masking tape to prevent gaps where the wrist could be exposed. For low-intensity UV sources, the requirement for UV protection can be waived if the exposure to personnel has been measured and shown to be within permissible exposure levels.
- Environmental / Ventilation Controls
- All operations involving powder or mists of ethidium bromide must be done in a fume hood. Check for proper operation of the fume hood prior to use.
- Special Handling Procedures & Storage Requirements
- Liquid: Store in the dark and the cold, preferably in a plastic container; away from strong oxidizing agents. Solid: Store at the designated area.
- Spill and Accident Procedures
- When working with ethidium bromide, try to minimize the potential for spills. Where practical, purchase ready-made stock solutions from chemical manufacturers in lieu of mixing your own solutions. If you prefer to mix your own solutions of ethidium bromide, protect yourself by doing this process in a fume hood. Perform all processes that generate ethidium bromide dust or mists inside the fume hood to minimize inhalation exposures. Prevent accidents by transporting small quantities of ethidium bromide in a secondary container instead of carrying large quantities.
- Spills of ethidium bromide solutions should be absorbed and decontaminated with soap and water. Avoid raising dust when cleaning up solid spills by mixing it with water and then absorbing the solution. All spill-cleanup materials and absorbents should be bagged or placed in a sealed container with a hazardous waste label.
- Some facilities use a hand-held UV lamp to check for residual ethidium bromide contamination following spill cleanup. A reddish-orange fluorescence can be detected under both "long" and "short" UV wavelengths. Users of handheld lamps should be aware that their ability to detect small spills is not guaranteed. The ease of detection depends upon a variety of factors including the chemical composition of the sample, the wavelength of the UV lamp, and the intensity of the lamp. The use of a hand-held UV lamp to detect traces of ethidium bromide may serve as an occasional check of laboratory practices, but it cannot substitute for good cleanliness and careful contamination control.
- Waste Disposal
- EH&S recommends that ethidium bromide waste be treated using special filters. These filters use ion-exchange resins and activated charcoal to remove the ethidium bromide from the solution. There are effective chemical treatments to destroy ethidium bromide, but filtering is an easier and safer choice.
- Powders, concentrated solutions, and grossly contaminated items are hazardous waste. Label with Hazardous Waste Label, accumulate according to requirements, and send in Chemical Collection Request or Routine Pickup request.
- Notify EH&S at 2252 of waste to be picked up from your laboratory’s Satellite Accumulation Area (SAA).
- Special Precautions for Animal Use (if applicable)
- Approval Required
- Principal Investigator/Responsible Person approval is required before use of this material.
- Decontamination
- Use copious amounts of soap and water.
- Designated Area
- Fume hood at _____________________ . Check that the fume hood is operating properly before starting the procedure.
- Labeling
- Whenever ethidium bromide is mixed and stored outside of its original container, it must be clearly marked with its concentration and a description of its hazards. Always use the full chemical name on the label.
- Training of Personnel
- All personnel are required to complete the Chemical Hygiene Plan training. Furthermore, all personnel shall read and fully adhere to this SOP when handling the chemical.
- Description
-
Flammable and Combustible Liquids SOP
Principal Investigator (PI) Approval is Required Prior to Performing this Procedure
Description
Various.
In most laboratory situations, the main flammability concerns will be liquids and gases, but solids (especially finely-divided materials allowed to become airborne) may also be flammable.
Potential Hazards
Flammability. Check the Safety Data Sheet (SDS) of the material for other hazards and follow appropriate SOPs.
Definitions –
- Flammable gas – a gas that, at 68°F or less and standard pressure, forms a flammable mixture with air at a concentration of 13% by volume or less OR that, at ambient temperature and pressure, forms a range of flammable mixtures with air wider than 12% by volume, regardless of the lower limit.
- Flammable liquid – a liquid having a flash point below 100°F.
- Flammable solid – a solid, other than a blasting agent or explosive, that (1) has an ignition temperature below 212°F, or (2) is capable of causing a fire through friction, absorption of moisture, or spontaneous chemical change, or (3) burns so vigorously and persistently as to create a serious hazard.
- Combustible liquid – a liquid having a flash point at or above 100°F (definition listed for storage considerations).
Engineering Controls
Work in a chemical fume hood if air concentrations above 10% of the lower flammable limit may be reached, if the chemical is irritating to the eyes and respiratory system, and/or is toxic by inhalation. (For toxic materials, also refer to the toxic gases, liquids, or powders/suspensions SOP.)
Work Practice Controls
- Know the location of the nearest fire extinguisher before beginning work.
- Use in the smallest practical quantities for the experiment being performed.
- Avoid using ignition sources (Bunsen burners, hot plates, electrical equipment with frayed or cracked wiring, etc.) and/or creating static electricity in areas where highly flammable chemicals are used.
- Ensure proper grounding. Be sure to ground metal containers when transferring flammable liquids.
- Keep containers of flammable chemicals closed at all times when not in use to prevent accumulation of flammable vapor concentrations.
Personal Protective Equipment (PPE)
- Wear standard nitrile laboratory gloves, lab coat, safety glasses, clothing that minimizes exposed skin, and close-toed shoes for all work with flammables. If working with flammable liquids that may splash, wear chemical splash goggles.
- If a liquid flammable is also toxic, check a glove guide for appropriate gloves and/or minimize glove contact with the liquid.
- Avoid wearing flammable clothing (such as many synthetics) when working with flammable materials.
Transportation and Storage
- Flammable chemicals should be stored in appropriate areas within the laboratory and away from any potentially incompatible materials.
- Transport flammables in secondary containment, preferably polyethylene or other non-reactive acid/solvent bottle carrier.
- Suitable fire control devices (such as fire extinguishers) must be available at locations where flammable or combustible liquids are stored. Contact EH&S at 509-963-2252 for the installation of appropriate devices.
- Open flames shall not be permitted in flammable liquid storage areas. A “No Open Flames” sign must be conspicuously posted in these areas.
- Flammable and combustible liquids must not be stored in a manner that hinders safe egress.
- If large quantities (>60 gallons) of flammable or combustible liquids are stored, a specially-designed storage room may be required. See the CWU Safety Manual Hazardous Materials Policy or contact EH&S at 509-963-2338 for more information.
- Store these materials in a separate room from water reactives.
- The total volume of flammable or combustible liquids outside of approved storage cabinets shall not exceed 5 gallons per 100 square feet.
- No more than 60 gallons of flammable and combustible liquids may be stored in any single flammable storage cabinet. All such storage cabinets must meet NFPA 30 requirements.
- The total stored volume of flammable and combustible liquids in approved storage cabinets shall not exceed 20 gallons per 100 square feet, with a maximum of 10 gallons per 100 square feet being flammable liquid (per definition above).
- Flammable liquids shall not be stored in unapproved or residential-type refrigerators. See the Policy Supplement on Storage of Flammable Chemicals in Refrigerators for more information.
- Flammable liquids may not be stored in cold rooms unless the lab has written verification from EH&S that the cold room was specifically designed for and has been maintained for the storage of flammable liquids.
- Secondary containment is recommended for liquids.
- Avoid storing on the floor.
Waste Disposal
Handle and store flammable wastes following the guidelines above while accumulating wastes and awaiting chemical waste pickup. Waste must be disposed of following your laboratory-specific chemical hygiene plan and the requirements of Central Washington University’s Chemical Waste Policy and the Laboratory Chemical Waste Management Practices.
Spill Procedures
On the CWU campus, “large” spills of hazardous materials and all mercury spills must be referred to the EH&S spill response team by calling 911 from a campus phone.
Training of Personnel
All personnel are required to complete the Chemical Hygiene Plan training. Furthermore, all personnel shall read and fully adhere to this SOP when handling the chemical.
-
Formalin and Paraformaldehyde SOP
Principal Investigator (PI) Approval is Required Prior to Performing this Procedure
Description
This SOP must be customized for each lab using formalin solution, paraformaldehyde solution, or paraformaldehyde solid. Use this section to describe the circumstances of use, including concentration and quantity.
Potential Hazards
- Formalin and paraformaldehyde solutions can emit formaldehyde gas, a known human carcinogen, and can irritate the eyes and skin.
- Working with paraformaldehyde powder (and, to a lesser extent, flakes or granules), can expose employees to paraformaldehyde dust, which is a strong irritant/sensitizer.
- Contact with these solutions or paraformaldehyde solids may also cause drying of the skin and/or allergic dermatitis.
The OSHA Permissible Exposure Limit for formaldehyde is 0.75 ppm for 8 hours or 2 ppm for 15 minutes. There is a substance-specific OSHA standard for formaldehyde and an action limit of 0.5 ppm.
Engineering Controls
- Work with concentrated (>4% formaldehyde/paraformaldehyde) solutions only in a chemical fume hood.
- Handle paraformaldehyde powder (and, preferably, granules or flakes) only in a chemical fume hood.
- Dilute solutions (<4% formaldehyde) may be used on the benchtop in small quantities.
- If there is any possibility that an employee's eyes may be splashed with solutions containing 0.1 percent or greater formaldehyde, an eyewash/drench hose must be available within the immediate work area for emergency use.
- If employees' skin may become splashed with solutions containing 1 percent or greater formaldehyde, for example, because of equipment failure or improper work practices, the OSHA formaldehyde standard requires a conveniently-located safety shower. Contact EH&S at extension 2338 to determine if a safety shower will be needed.
Work Practice Controls
- Laboratory-specific written procedures are required for formalin and paraformaldehyde, including a designated work area. Designate an area for working with concentrated formalin, concentrated paraformaldehyde solutions, and paraformaldehyde solid, and label it as such.
- Keep containers closed as much as possible.
- Use in the smallest practical quantities for the experiment being performed.
- If you are weighing paraformaldehyde powder and the balance cannot be located in a fume hood or BSC, tare a container then add powder in the hood and cover before returning to the balance to weigh the powder.
- Labs handling moderate to large quantities of formaldehyde-containing solutions on a regular basis should contact EH&S at extension 2252 for assessment of exposure. Areas that handle only small (100 ml or less) pre-filled specimen containers, or that work with formaldehyde-containing solutions exclusively in a functioning chemical fume hood, would have low potential for overexposure, but should contact Risk management if there are concerns.
Personal Protective Equipment (PPE)
The level of skin and eye protection should be selected based on the potential for splashing and other forms of exposure.
Minimum potential for splash & exposure:
- Chemical splash goggles
- Single pair of nitrile, neoprene, PVC (vinyl), butyl, or VitonTM gloves
- Immediately replace with new gloves when splash occurs.
- Protective clothing (e.g. non-porous lab coat, impervious sleeves; closed-toed impervious shoes)
When using or transferring large quantities:
- Chemical splash goggles
- Face shield (if not working in a fume hood or if the hood’s sash is not in the down position)
- Double nitrile, neoprene, PVC (vinyl) ), butyl, or VitonTM gloves
- Immediately replace with new gloves when splash occurs.
- Chemical-resistant apron/smock/lab coat (PE or PVC)
- Avoid using the traditional cotton-polyester white lab coat, which readily collects/absorbs compounds.
- Protective clothing (e.g. non-porous sleeves, closed-toed impervious footwear)
(OSHA requires that all contact of the eyes and skin with liquids containing 1 percent or more formaldehyde be prevented by the use of chemical protective clothing made of material impervious to formaldehyde and the use of other personal protective equipment, such as goggles and face shields, as appropriate to the operation.)
ADDITIONAL PRECAUTIONS
- Reacts violently with nitrogen dioxide, perchloric acid/aniline mixtures, and nitromethane.
- Reacts with HCI to form the potent carcinogen, bis-chloromethyl ether.
- Keep away from heat, sparks, and flame.
- Keep separate from oxidizing agents, alkalis, inorganic acid, ammonia, phenol, isocyanates, peracids (non-chlorine bleaching agents such as H2O2), and anhydrides.
- Store containers of formaldehyde in secondary containers in areas separate from the incompatibles.
Transportation and Storage
- Transport formaldehyde solutions in secondary containment, preferably polyethylene or other non-reactive acid/solvent bottle carrier.
- Keep the container in a cool, well-ventilated area.
- Keep the container tightly closed and sealed until ready for use.
- Store in secondary containment with flammables, away from oxidizers, reducing agents, metals, and acids.
- Keep containers of PFA solid away from water.
- Avoid storing on the floor.
Waste Disposal
Formalin and paraformaldehyde solutions and powders must be disposed of following your laboratory-specific chemical hygiene plan and the requirements of Central Washington University’s Chemical Waste Policy.
Exposures/Unintended Contact
- Flush exposed eyes or skin with water for at least 15 minutes, and then seek medical attention. If there is respiratory irritation associated with exposure, call 911.
- Follow-up medical attention should be sought.
Spill Procedures
Employees in the area should be prepared to clean up minor spills, including most spills confined to the chemical fume hood. Wearing double nitrile gloves, splash goggles, face shield, and lab coat (and impermeable apron, if available); use absorbent pads to absorb spilled material. (For small spills of solid PFA, dampen the absorbent pad with methanol before placing it over the spilled material and allowing it to sit for a few minutes before wiping it up.) Contaminated PPE and clean-up materials must be placed in a clear plastic bag or compatible container for pick-up by Risk Management.
NOTE: If there is respiratory irritation associated with exposure, remove all persons from the contaminated area and call 911.
Chemical Spill:
- For small spills, 25 ml/25 g or less, follow the chemical spill response guidelines above. Don protective clothing, extinguish all ignition sources and carefully apply vermiculite or other appropriate spill-absorbent material to the spill. Place in appropriate containers for disposal.
- For a large spill, vacate the lab, deny further entry, and call EHS for assistance.
Fire:
- Toxic vapors, including irritating gaseous formaldehyde, may be given off in a fire. In the event of a fire, evacuate and bar further entry.
Report all emergencies, suspicious activity, injuries, spills, and fires to the University Campus Police Department by calling 911.
Training of Personnel
- All laboratory personnel are required to attend a general laboratory safety session that includes an introduction to general chemical safety.
- Training on lab-specific procedures is required for all personnel working with these materials and must be documented (topics covered, date, employee names, and signatures).
- Furthermore, all employees working with formalin or paraformaldehyde solutions or PFA powder are required to take OSHA-required Formaldehyde training. Those required to take this training and authorized to work with these materials are indicated here:
All personnel shall read and fully adhere to the laboratory-specific SOP for formalin, paraformaldehyde, and paraformaldehyde solutions, and shall document that they have read it by signing and dating the SOP.
-
Strong Alkalines SOP
Principal Investigator (PI) Approval is Required Prior to Performing this Procedure
Description
An alkali is a basic, ionic salt of an alkali metal or alkaline earth metal element that dissolves in water. A strong alkali is an alkali that ionizes completely when dissolved in water. Chemicals that fall under this SOP (but are not limited to) include:
- Sodium hydroxide (CAS No. 1310-73-2)
- Potassium hydroxide (CAS No. 1310-58-3)
- Calcium hydroxide (CAS No. 1305-62-0)
Potential Hazards
- Extremely corrosive (causes burns to any area of contact – skin, eyes, mucous membranes)
- Irritant (skin, eyes, and respiratory tract)
- Unlike acids, hydroxides do not coagulate protein which impedes penetration. Metal hydroxide may not be immediately painful during skin penetration, producing severe and slow-healing burns.
Engineering Controls
All operations involving sodium hydroxide should be carried out in a chemical fume hood with the sash in the down position, between your chest and what you are handling in the hood.
- If the hood’s sash cannot be adjusted horizontally, protective eyewear is required (see “Required Personal Protective Equipment”)
Work Practice Controls
- Avoid heat sources and moisture.
- Reaction with aluminum or magnesium generates flammable and potentially explosive hydrogen gas; reaction with nitromethane and nitrophenols produces shock-sensitive explosive salts.
- Do not mix with acids or organic materials.
- When mixing with water, always add caustics/alkalines slowly to the water and stir continuously. Never add water in limited quantities to solid hydroxides.
Personal Protective Equipment (PPE)
(Refer to your lab’s PPE Assessment Report, supplemented with information here)
- Chemical splash goggles. Face shield, optional.
- Only applicable if not working in a fume hood or if the hood’s sash is not in the down position.
- Double nitrile, neoprene, or latex gloves
- Immediately replace with new gloves when contamination occurs.
- Chemical-resistant apron/smock/lab coat (PE or PVC) that covers limbs
- Avoid using the traditional cotton-polyester white lab coat, which readily collects/absorbs compounds.
- Closed-toed, impervious footwear
Decontamination
- Wipe any residual sodium hydroxide off of balance after use. Neutralize contamination, as necessary.
- Regular or intermittent use of strong alkalines warrants on-site supplies – neutralizing powder or liquid, absorbent powder, and personal protective equipment/garb. Also, see neutralizing powder in the spill clean-up kit located in your building.
Waste Disposal
Handle and store alkaline wastes following the guidelines above while accumulating wastes and awaiting chemical waste pickup. Waste must be disposed of following your laboratory-specific chemical hygiene plan and the requirements of Central Washington University’s Chemical Waste Policy and the LaboratoryChemical Waste Management Practices.
Spill Procedures
- For small spills, follow the chemical spill response guidelines above. Don protective clothing and carefully apply neutralization powder or liquid, whichever is most appropriate, to the spill. Allow time to neutralize, and then apply liquid absorbent pellets or powder.
- For a large spill, vacate the lab, deny further entry, and call EH&S (509-963-2252) for assistance.
Training of Personnel
All personnel are required to complete the Chemical Hygiene Plan training. Furthermore, all personnel shall read and fully adhere to this SOP when handling the chemical.
-
Mineral Acid SOP
Principal Investigator (PI) Approval is Required Prior to Performing this Procedure
Description
A mineral acid is defined as a water-soluble acid derived from inorganic minerals by chemical reaction as opposed to organic acids (e.g. acetic acid, formic acid). Chemicals that fall under, but are not limited to, this SOP include:
- Boric acid (CAS No. 10043-35-3)
- Chromic acid (CAS No. 1333-82-0)
- Hydrochloric acid (CAS No. 7647-01-0)
- Hydrofluoric acid (CAS No. 7664-39-3)
- Nitric acid (CAS No.7697-37-2)
- Phosphoric acid (CAS No. 7664-38-2)
- Sulfuric acid (CAS No. 7664-93-9)
Potential Hazards
- Corrosive – causes severe eye and skin burns; can cause digestive and respiratory tract burns
- Irritant – eye, skin, respiratory tract, digestive tract
Additional Comments:
- Nitric acid – strong oxidizer
- Sulfuric acid – water reactive; strong inorganic acid mists containing sulfuric acid can cause cancer
- Hydrofluoric acid – causes severe burns, which may not be immediately painful or visible - symptoms may be delayed 8 hours or longer
Engineering Controls
All operations involving concentrated mineral acids should be carried out in a chemical fume hood with the sash in the down position, between your chest and what you are handling in the hood.
Personal Protective Equipment (PPE)
(Refer to your lab’s PPE Assessment Report, supplemented with information here)
- Chemical splash goggles
- Face shield
- Only applicable if not working in a fume hood or if the hood’s sash is not down.
- Long neoprene or thick butyl rubber gloves (when used with hydrofluoric acid)
- Double nitrile, neoprene, or PVC (vinyl) gloves (except when used with hydrofluoric acid)
- Immediately replace with new gloves when splash occurs.
- Chemical-resistant apron/smock/lab coat (rubber, neoprene, or PVC), reusable or disposable.
- Avoid using the traditional cotton-polyester white lab coat, which readily collects/absorbs compounds.
- Protective clothing (e.g., impervious sleeves, closed-toed impervious footwear)
ADDITIONAL PRECAUTIONS
- When diluting, the acid should always be added slowly to water and in small amounts. Never use hot water and never add water to the acid. Water added to acid can cause uncontrolled boiling and splashing.
- Reaction with certain metals generates flammable and potentially explosive hydrogen gas.
- Avoid mixing nitric acid with organics. This can result in an explosion or fire.
- Stock fresh calcium gluconate, in a tube, to counter the immediate effects of hydrofluoric acid on the skin, and tissue (after 5 minutes of flushing with tepid water); then, seek immediate medical attention.
Storage
- Bottles of mineral acids should be stored together in an acid (corrosive) cabinet.
- Nitric acid, a strong oxidizer, should be stored separately in a chemically resistant secondary container within an acid cabinet. This could be a polyethylene, PYREX or Nalgene tray or pan. It can also be stored in its own acid cabinet.
- Mineral acids should be stored separately from oxidizing agents, organic materials, and combustible materials.
- Avoid storing ammonium hydroxide and strong mineral acids in the same cabinet.
- Containers of hydrochloric acid and sulfuric acid should be stored in secondary plastic trays to avoid corrosion of metal storage shelves due to drips or spills; containers of hydrofluoric acid should be stored in secondary containers made of polyethylene.
Waste Disposal
Handle and store mineral acid wastes following the guidelines above while accumulating wastes and awaiting chemical waste pickup. Waste must be disposed of following your laboratory-specific chemical hygiene plan and the requirements of Central Washington University’s Chemical Waste Policy and the Laboratory Chemical Waste Management Practices.
Exposures/Unintended Contact
- If skin contact occurs, immediately remove contaminated clothing and rinse with water for at least 15 minutes.
- For eye exposures, immediately rinse eyes with copious amounts of water for at least 15 minutes, while occasionally lifting upper and lower lids, then promptly seek medical attention.
- If large amounts of vapors are inhaled, move the person to fresh air immediately and seek medical attention.
- If nitric acid is ingested, seek medical attention immediately.
Spill Procedures
(Refer to the Emergency Response Guide posted in each lab, supplemented with information here)
- For small spills, follow the chemical spill response guidelines above. Don protective clothing and carefully apply acid-neutralization powder or liquid, whichever is most appropriate, to the spill. Allow time to neutralize, and then apply liquid absorbent pellets or powder. Once the absorbent has been removed, wash the contaminated area with sodium bicarbonate and water.
- For a large spill, vacate the lab, deny further entry, and call EH&S for assistance.
- In the event of a fire, evacuate and bar further entry. Activate the fire alarm and leave the building. May emit toxic fumes under fire conditions.
Report all emergencies, suspicious activity, injuries, spills, and fires to the University Campus Police Department by calling 911.
Training of Personnel
All personnel are required to complete the Chemical Hygiene Plan training. Furthermore, all personnel shall read and fully adhere to this SOP when handling the chemical.
-
Nitric Acid - Concentrated SOP
Principal Investigator (PI) Approval is Required Prior to Performing this Procedure
Description
This standard operating procedure outlines the handling and use of concentrated nitric acid. Review this document and supply the information required in order to make it specific to your laboratory. In accordance with this document, laboratories should use appropriate controls, personal protective equipment, and disposal techniques when handling nitric acid.
Potential Hazards
- Nitric acid is a very strong oxidizer that can ignite on contact or react explosively with many organic and inorganic substances.
- Contact with easily oxidizable substances (including many organic substances such as acetone, acetonitrile, various alcohols, dichloromethane, DMSO, and many others) may result in fires or explosions.
- Nitric acid also reacts violently with many inorganic substances including various bases, reducing agents, ammonia, and alkali metals, among others. Many reactions will yield toxic gases, including nitrogen dioxide (NO2) – see next bullet.
- Concentrated nitric acid can release vapors and toxic gases (including NO2), which can cause moderate to severe health effects, especially irritation to the eyes, skin, respiratory tract, and other mucosal membranes.
- If concentrated nitric acid contacts the skin, it can cause severe burns. Dilute concentrations that contact skin can cause mild irritation.
- Contact with eyes can cause severe burns and permanent eye damage.
- If high concentrations of nitric acid are inhaled, severe respiratory irritation can develop, along with possible delayed effects such as pulmonary edema, which can be fatal.
- Though not likely, ingestion of nitric acid can cause severe corrosion and burning of the mouth, esophagus, and stomach. As little as 10 ml of ingested nitric acid can be fatal.
- For further safety information, refer to Prudent Practice’s Laboratory Chemical Safety Summary for Nitric Acid.
- The OSHA Permissible Exposure Limit for nitric acid is 2 ppm (8 hours). The American Conference of Governmental Industrial Hygienists recommends a short-term exposure limit (15 minutes) of 4 ppm and an 8-hour limit of 2 ppm.
Engineering Controls
- An eyewash and safety shower must be available in the immediate work area for any work with nitric acid.
- When working with nitric acid, always work in a clean fume hood that contains NO organic materials with the sash closed while reactions are in progress.
- Always use containers/glassware free from organic materials (and other incompatibles) for work with nitric acid.
- If mists are generated either mechanically or from vapor, work must be performed in a chemical fume hood to avoid inhalation.
Work Practice Controls
- If other specific written procedures are required for your work with nitric acid (e.g. heated process, large quantities), you must list them here or attach a step-by-step procedure. (If no further procedures are needed beyond those listed in this template, you can delete this bullet.)
- Work should be done in a way that avoids hand/glove contact with nitric acid; it should be noted that nitric acid penetrates standard nitrile gloves in 5 minutes or less.
- If gloves come in contact with nitric acid through a splash (or otherwise), they should be removed and changed immediately.
- Once work with nitric acid is complete, decontaminate the area by wiping it down with a soap and water solution.
Personal Protective Equipment (PPE)
- Goggles, lab coat, closed-toed shoes, double gloves (nitrile), or chemical-resistant gloves (approved for contact with nitric acid) if there is an increased risk of glove contact. If neoprene gloves are available, they offer better protection than nitrile.
- Face shield and acid-resistant apron are recommended if working with a larger volume (>200ml).
- Latex gloves are NOT recommended for work with nitric acid (they offer little to no protection due to easy chemical penetration).
- If contact with gloves in unavoidable, gloves rated for work with nitric acid must be used. Thicker neoprene gloves typically have the best glove ratings for prolonged nitric acid exposure (e.g. Chloroflex II from Best Glove Company).
Transportation and Storage
- Nitric acid should be stored in secondary containment in a well-ventilated area that is separated from organics and other combustible materials and incompatibles.
- Ensure primary and secondary containment is free from organic chemicals/solvents.
- Transport corrosives in secondary containment, preferably polyethylene or other non-reactive acid/solvent bottle carrier.
- Store below eye level.
- Store away from metal (unless the metal has a corrosion-proof coating), and do not store under the sink.
- Avoid storing on the floor.
Waste Disposal
Handle and store nitric acid wastes following the guidelines above while accumulating wastes and awaiting chemical waste pickup. Waste must be disposed of following your laboratory-specific chemical hygiene plan and the requirements of Central Washington University’s Chemical Waste Policy and the Laboratory Chemical Waste Management Practices.
Exposures/Unintended Contact
- If skin contact occurs, immediately remove contaminated clothing and rinse with water for at least 15 minutes.
- For eye exposures, immediately rinse eyes with copious amounts of water for at least 15 minutes, while occasionally lifting upper and lower lids, then promptly seek medical attention.
- If large amounts of vapors are inhaled, move the person to fresh air immediately and seek medical attention.
- If nitric acid is ingested, seek medical attention immediately.
Spill Procedures
On the CWU campus, “large” spills of hazardous materials and all mercury spills must be referred to the EH&S spill response team by calling 911 from a campus phone.
In the case of a small spill (<200 ml) contained in the fume hood, neutralize the spill by gradually adding alkaline material (sodium carbonate, lime) from the edges of the spill towards the center. Test the pH of the spilled material and continue neutralizing until the pH reaches the 6-9 range. Absorb with an inert material (vermiculite, dry sand). Do NOT use combustible materials, such as sawdust, to absorb nitric acid spills! Place materials in a chemical waste container and dispose of them appropriately. Appropriate chemical-resistant gloves should be used when cleaning up a spill due to possible prolonged glove contact with nitric acid. After the spill has been completely absorbed, wipe the contaminated area down with a soap and water solution.
If nitric acid is spilled outside of the fume hood, call the spill response team for assistance.
Report all emergencies, suspicious activity, injuries, spills, and fires to the University Campus Police Department by calling 911.
Training of Personnel
All personnel are required to complete the Chemical Hygiene Plan training. Furthermore, all personnel shall read and fully adhere to this SOP when handling the chemical.
-
Oxidizer SOP
Principal Investigator (PI) Approval is Required Prior to Performing this Procedure
Description
Common oxidizers include Hydrogen peroxide, Nitric acid, Nitrate and Nitrite compounds, Perchloric acid, and Perchlorate compounds, and Hypochlorite compounds, such as household bleach. Oxidizers have a wide variety of applications including cleaners and disinfectants, agricultural fertilizers, rocket propellant and fuel, and explosives.
Important Definitions:
- Oxidizing liquid- a liquid which, while in itself is not necessarily combustible, may generally by yielding oxygen, cause or contribute to the combustion of other material. Hydrogen peroxide, nitric acid, and nitrate solutions are examples of oxidizing liquids commonly found in a laboratory.
- Oxidizing solid- a solid which, while in itself not necessarily combustible, may generally by yielding oxygen, cause or contribute to the combustion of other material.
Potential Hazards
Oxidizer. Keep away from heat. Keep away from clothing and other combustible materials. Take any precautions to avoid mixing with combustibles. Store away from combustibles. Oxidizers can have other associated hazards, such as corrosive or toxic (e.g., Nitric acid, Sodium nitrite). Make sure that all of the potential hazards are understood before handling any chemical.
[INSERT IMAGE globally-harmonized-system-OXIDIZER-symbol.JPEG]
Engineering Controls
The use of oxidizing liquids and solids should be conducted in a properly functioning chemical fume hood whenever possible. The chemical fume hood must be approved and certified by EH&S and have a face velocity between 85 – 125 feet per minute.
Personal Protective Equipment (PPE)
Respirator Protection:
If oxidizing liquids or solids are being used outside of a chemical fume hood, respiratory protection may be required. If this activity is absolutely necessary, contact EH&S at 509-963-2252 so that a respiratory protection analysis can be performed. Respirators should be used under any of the following circumstances:
- As a last line of defense (i.e., after engineering and administrative controls have been exhausted).
- When the Permissible Exposure Limit (PEL) has exceeded or when there is a possibility that PEL will be exceeded.
- Regulations require the use of a respirator.
- An employer requires the use of a respirator.
- There is potential for harmful exposure due to an atmospheric contaminant (in the absence of PEL)
- As PPE in the event of a chemical spill clean-up process
Lab personnel intending to use/wear a respirator mask must be trained and fit-tested by EH&S at 509-963- 2252. This is a regulatory requirement.
Hand Protection:
Gloves must be worn. Use proper glove removal techniques to avoid any skin contact. Nitrile gloves are recommended. Check the resources below for the most suitable glove.
NOTE: Consult with your preferred glove manufacturer to ensure that the gloves you plan on using are compatible with the specific oxidizing liquids or solids being used.
Eye Protection:
ANSI-approved properly fitting safety glasses or chemical splash goggles are required. A face shield may also be appropriate depending on the specific application.
Skin and Body Protection:
Laboratory coats must be worn and be appropriately sized for the individual and buttoned to their full-length Laboratory coat sleeves must be of sufficient length to prevent skin exposure while wearing gloves. Personnel should also wear full-length pants or equivalent, and close-toed shoes. Full-length pants and close-toed shoes must be worn at all times by all individuals that are occupying the laboratory area. The area of skin between the shoe and ankle should not be exposed.
Hygiene Measures:
Wash thoroughly and immediately after handling. Rinse immediately contaminated clothing and skin with plenty of water before removing clothes.
Special Storage Requirements
- Do not over-purchase; only purchase what can be safely stored in the laboratory.
- Avoid contact with skin, eyes, and inhalation. Avoid inhalation of vapor or mist. Avoid the formation of dust.
- Keep away from combustible materials. Keep away from sources of ignition - No smoking.
- Keep containers tightly closed. Store in a cool, dry, and well-ventilated area away from incompatible substances such as flammable and combustible liquids.
- Keep cool and protected from sunlight.
- Opened containers of oxidizing liquids must be carefully resealed and kept upright to prevent leakage.
- Carefully follow the manufacturer’s instructions if oxidizing liquid needs to be vented during storage.
Waste Disposal Label Waste:
When possible, do not mix oxidizer waste streams with flammable or combustible waste. Make sure the waste container(s) is properly labeled; the label should indicate all of the contents of the container.
Store Waste:
Store hazardous waste in closed containers, and in a designated area.
Dispose of Waste:
Complete a Chemical Waste Pickup Request Form to arrange for disposal by EH&S. Call EH&S at 509-963-2252 or visit the EH&S webpage for questions. No oxidizing liquids or solids are permitted to be poured down the drain.
Safety Data Sheet (SDS)
A current copy of the SDS for the specific oxidizing liquid or solid being used must be made available to all personnel working in the laboratory at all times. To obtain a copy of the SDS, contact the chemical manufacturer or EH&S at 509-963-2338. Many manufacturers’ SDSs can be found online on websites such as Sigma-Aldrich or Siri MSDS Index.
Protocol/Procedure (Additional lab protocol may be added here)
- Use in the smallest practical quantities for the experiment being performed.
- Work must be conducted in a chemical fume hood if the chemical is irritating to the eyes or respiratory system, and/or is toxic by inhalation.
- Containers should remain closed when not in use.
- Containers should be labeled appropriately. The label should indicate the name of the chemical(s) in the container. Avoid using chemical abbreviations (acceptable if a legend is present in the lab) and formulae.
- Containers should be in good condition and compatible with the material.
- Avoid using ignition sources (flame burners or any open flame source, hot plates, electrical equipment with frayed or cracked wiring, etc.) and/or creating static electricity in areas where oxidizing chemicals are being used.
- Transport all oxidizing liquids and solids in secondary containment, such as polyethylene or other non-reactive acid/solvent bottle carrier.
- Oxidizers must be segregated from incompatible materials such as flammable and combustible materials. Incompatibilities will be noted in Section 10 of the SDS, “Stability and Reactivity”.
Training of Personnel
All personnel are required to complete the Chemical Hygiene Plan training. Furthermore, all personnel shall read and fully adhere to this SOP when handling the chemical.
-
Perchloric Acid SOP
Principal Investigator (PI) Approval is Required Prior to Performing this Procedure
Description
Perchloric acid is an inorganic compound with the formula HClO4. Usually encountered as an aqueous solution, this colorless compound is a strong acid comparable in strength to sulfuric acid and nitric acid. It is a powerful oxidizer, but its aqueous solutions of up to 70% are remarkably inert, only showing strong acid properties and no other oxidizing properties. Above concentrations of approximately 70%, the speed of oxidizing reactions rapidly increases with increasing acid concentration. It is useful for preparing perchlorate salts, especially ammonium perchlorate, an important rocket fuel. Perchloric acid is also dangerously corrosive and readily forms explosive mixtures.
Perchloric acid is mainly produced as a precursor to ammonium perchlorate, which is used as rocket fuel. The growth in rocketry has led to increased production of perchloric acid. Several million kilograms are produced annually. It is one of the strongest Brønsted-Lowry acids. Despite hazards associated with the explosiveness of its salts, the acid is often preferred in certain syntheses.
Potential Hazards
EMERGENCY OVERVIEW: Appearance: clear, colorless liquid. Causes digestive and respiratory tract burns. Causes eye and skin burns. Perchloric acid is a strong oxidizer and is corrosive to metal. Contact with other materials may cause a fire. Heating may cause an explosion. Contact with other materials may cause an explosion.
Highly important danger information!
In addition to being a corrosive liquid, while not combustible, under some circumstances, perchloric acid may act as an oxidizer and/or present an explosion hazard. Perchloric crystals, or perchloric acid in crystalline form, are an extremely dangerous inorganic compound. The crystals are sometimes formed due to condensation inside of ventilation hoods in chemical labs or in bottles stored for extended periods in the lab. Among the principal hazards are that the perchlorite crystals are subject to exploding on impact.
Organic materials are especially susceptible to spontaneous combustion if mixed or contacted with perchloric acid. Under some circumstances, perchloric acid vapors form perchlorates in duct work, which are shock sensitive.
Target Organs: Eyes, thyroid, skin, mucous membranes.
Potential Health Effects:
- Eye: Causes eye burns.
- Skin: Causes skin burns.
- Ingestion: Harmful if swallowed. Causes gastrointestinal tract burns.
- Inhalation: Causes severe respiratory tract irritation with possible burns.
- Chronic: Prolonged or repeated skin contact may cause dermatitis.
Engineering Controls
Facilities storing or utilizing this material should be equipped with an eyewash facility and a safety shower. Any procedure involving heating of perchloric acid must be conducted in a perchloric acid fume hood, with the sash down. No organic materials should be stored in the perchloric acid hood.
Personal Protective Equipment (PPE)
- Eyes: Wear chemical goggles and face shield. Use chemical splash and impact-rated goggles.
- Skin: Natural Rubber, Natural Rubber, PVC, Nitrile, or Viton gloves must be worn while handling perchloric acid
- Clothing: Wear long pants, closed-toed shoes, and a lab coat
- Respirators: A respiratory protection program that meets OSHA's 29 CFR 1910.134 and ANSI Z88.2 requirements or European Standard EN 149 must be followed whenever workplace conditions warrant a respirator's use.
First Aid Procedures
- Eyes: In case of contact, immediately flush eyes with plenty of water for at least 15 minutes. Get medical aid immediately.
- Skin: Destroy contaminated shoes. In case of contact, immediately flush skin with plenty of water for at least 15 minutes while removing contaminated clothing and shoes. Get medical aid immediately. Wash clothing before reuse.
- Ingestion: If swallowed, do NOT induce vomiting. Call the Washington Poison Control Center at 1- 800-222-1222. Get medical aid immediately. If the victim is fully conscious, give a cupful of water. Never give anything by mouth to an unconscious person.
- Inhalation: If inhaled, remove to fresh air. If not breathing, give artificial respiration. If breathing is difficult, give oxygen. Get medical aid.
Notes to Physician: Treat symptomatically and supportively.
Handling and Storage
- Handling: Wash thoroughly after handling. Remove contaminated clothing and wash it before reuse. Use spark-proof tools and explosion-proof equipment. Avoid contact with clothing and other combustible materials. Do not get on the skin or in the eyes. Do not ingest or inhale. Use only with adequate ventilation. Do not allow perchloric acid to come into contact with strong dehydrating agents (concentrated sulfuric acid, anhydrous phosphorous pentoxide, etc.). Keep the quantities of perchloric acid handled at the bare minimum for safety. Perchloric acid should be handled in a masonry building with concrete or tile floors. Handling acid on wooden floors is dangerous, especially after the acid has dried. The wooden floor will then become sensitive to ignition by friction. Perchloric acid mist and vapor can condense in ventilation systems to form metallic perchlorates, which can be explosive. Inform laundry personnel of contaminant's hazards.
- Storage: Do not store near combustible materials. Store in a tightly closed container. Store in a cool, dry, well-ventilated area away from incompatible substances. Avoid storage on wood floors. Perchloric acid should be stored segregated from all other chemicals & inside secondary containment (such as a Pyrex baking dish). It must not be stored near organic acids, near bases, or near other organic or flammable material. Shelves and floor material should be non-combustible and acid-resistant. Protect from freezing.
Waste Disposal
Waste disposal procedures:
- A Hazardous Waste Tag must be placed on each hazardous waste container upon start of accumulation.
Hazardous Waste Storage:
- Hazardous waste must be transferred to EH&S for disposal within 90 days of being generated.
- Waste containers must be in secondary containment at all times to adequately contain the contents of the container/spilled materials.
- Hazardous waste must always be appropriately labeled with a waste tag at all times.
- Containers must be closed when not in use.
- Storage of hazardous waste in fume hoods or under sinks is not recommended.
- Hazardous waste that meets the quantity threshold of 55 gallons of hazardous waste or 1 quart of extremely hazardous waste1 must be transferred to EH&S for disposal within 3 days of reaching these set volumes.
- Report damaged containers to EH&S. EH&S can provide assistance to transfer the contents to an appropriate container.
- Mark storage areas according to the type of chemicals kept there (e.g. “Corrosive”, “Flammable”, etc.).
- Containers should be inspected weekly for signs of leaks, corrosion, or deterioration. Hazardous Waste Disposal:
- Don't dispose of chemicals down the drain!
- Don't dispose of chemicals via trashcans.
- Don't use hoods to intentionally evaporate chemicals.
- Transport the hazardous waste to your designated pick-up location using a sturdy cart and secondary containment.
Spill Procedures
Chemical Spill Dial 911
- Spill – Clean up perchloric acid spills immediately, observing precautions in the Protective Equipment section. Remove all sources of ignition. Absorb spill using an absorbent, non-combustible material such as earth, sand, or vermiculite. Do not use combustible materials such as sawdust. Flush the spill area with water. Wet area to prevent drying out. Provide ventilation. Keep combustibles (wood, paper, oil, etc.,) away from spilled material. Keep unnecessary and unprotected personnel away. Use only non-sparking tools and equipment. The spill may be carefully neutralized with soda ash (sodium carbonate).
- Small (<1 L) – If you have the training, you may assist in the clean-up effort. Use appropriate personal protective equipment and clean-up material for chemicals spilled. Double bag spill waste in clear plastic bags, label and take to the next chemical waste pick-up.
- Large (>1 L) – Dial 911 and EH&S at extension 2338 for assistance.
- Chemical Spill on Body or Clothes – Remove clothing and rinse the body thoroughly in the emergency shower for at least 15 minutes. Seek medical attention. Notify the supervisor and EH&S at extension 2252 immediately.
- Chemical Splash Into Eyes – Immediately rinse the eyeball and inner surface of the eyelid with water for 15 minutes by forcibly holding the eye open. Seek medical attention. Notify the supervisor and EH&S at extension 2252 immediately.
Training of Personnel
All personnel are required to complete the Chemical Hygiene Plan training. Furthermore, all personnel shall read and fully adhere to this SOP when handling the chemical.
-
Peroxide Forming Compounds (PFC) SOP
Principal Investigator (PI) Approval is Required Prior to Performing this Procedure
Description
This standard operating procedure outlines the handling and use of peroxide-forming chemicals. Review this document and supply the information required in order to make it specific to your laboratory. In accordance with this document, laboratories should use appropriate controls, personal protective equipment, and disposal techniques when handling peroxide-forming chemicals.
Potential Hazards
Peroxide Formation
Peroxide formation in common laboratory chemicals is caused by an autoxidation reaction. The reaction can be initiated by light, heat, introduction of a contaminant, oxygen or the loss of an inhibitor. Some chemicals have inhibitors such as BHT (butylated hydroxytoluene), hydroquinone, and diphenylamine to slow peroxide formation. Most organic peroxide crystals are sensitive to heat, shock, or friction, and their accumulation in laboratory reagents has resulted in numerous explosions. For this reason, it is important to identify and control chemicals that form potentially explosive peroxides.
Peroxide Forming Compounds
In general, the more volatile the compound, the greater its hazard, since the evaporation of the compound allows the peroxide to concentrate. Peroxide accumulation is a balance between peroxide formation and degradation. Refer to the tables below for some common peroxide-forming chemicals and testing procedures.
Organic peroxide-forming materials can form shock-sensitive organic peroxide crystals over time or upon exposure to air. Also check each material’s SDS to determine if a chemical can form peroxides, and to check for other hazards.
Useful Peroxide Forming Materials Links:
- Kelly, R. J., "Review of Safety Guidelines for Peroxidizable Organic Chemicals", Chem. Health Saf. 1996, 3(5), 28-36
- Jackson, H. L.; McCormack, W. B.; Rondestvedt, C. S.; Smeltz, K. C.; Viele, I. E. J. Chem. Educ. 1970, 47(3), A175-88
- Clark, D. E., "Peroxides and Peroxide Forming Compounds", Chem. Health Saf. 2001, 8(5), 12-21
- National Safety Council, Recognition and Handling of Peroxidizable Compounds, 1987, Data Sheet I-655-Rev. 87
- National Research Council, Prudent Practices in the Laboratory: Handling and Disposal of Chemicals; National Academy Press: Washington, D. C., 1995; pp. 162-163.
- Kelley, R. J., "Peroxidizable Organic Chemicals", Handbook of Chemical Health and Safety, Chapter 52, ACS, 2001
NOTE: This is not an exhaustive list. Users must consult the chemical’s SDS and/or other sources of information for the chemicals used (and stored) to determine their peroxide-forming potential.
Peroxidizable Chemicals List
List A: Chemicals that form explosive levels of peroxides without concentration (3 months)1
- Butadiene2
- Chloroprene2
- Divinyl Acetylene
- Isopropyl Ether
- Potassium Metal
- Sodium Amide
- Tetrafluoroethylene2
- Vinylidene Chloride
List B: Chemicals that form explosive levels of peroxides on concentration (12 months)1
- 1,1-Dimethoxymethane
- 1,2-Epoxy-3-isopropoxy propane
- 1,2-Dibenzyloxyethane
- 1-Phenylethanol
- 2-Butanol
- 2-Hexanol
- 2-Methyl-1-butanol
- 2-Penten-1-ol
- 2-Phenylethanol
- 2-Propanol
- 4-Heptanol
- 4-Methyl-2-pentanol
- 4-Penten-1-ol
- Acetal
- Acetaldehyde
- Allyl Ether
- Benzyl alcohol
- Benzyl n-butyl Ether
- Benzyl Ether
- Benzyl Ethyl Ether
- Benzyl 1-naphthyl Ether
- Cumene
- Cyclohexene
- Cyclooctane
- Decahydronapthalene
- Diacetylene
- Diallyl Ether
- Dicyclopentadiene
- Diethoxymethane
- Diethyl acetal isoamyl benzyl
- ether
- Diethylene Glycoldimethyl Ether (diglyme)
- Dimethoxymethane
- Di-n-propoxymethane
- Dioxane
- Diethyl Ether
- Ethylene Glycol Dimethyl Ether
- Isoamyl Ether
- Isophorone
- Methy Isobutyl Ketone
- Methyl Acetylene
- Methylcyclopentane
- Other secondary alcohols
- p-Dibenzyloxybenzene
- p-Isopropoxypropionitrile
- Tetrahydrofuran
- Tetrahydronapthalene
- Vinyl Ethers
List C: Chemicals that may autopolymerize as a result of peroxide accumulation (12 months)1,3,4
- Acrylic Acid
- Acrylonitrile
- Butadiene2
- Chloroprene2
- Chlorotrifluoroethylene
- Methyl Methacrylate
- Styrene
- Tetrafluoroethylene2
- Vinyl Acetate
- Vinyl Acetylene
- Vinyl Chloride
- Vinyl Pyridine
- Vinyladiene chloride
- Safe storage periods are given for an open container of each class of peroxidizable material. Unopened containers from the manufacturer have a safe storage period of 18 months.
- When stored in liquid form these chemicals may form explosive levels of peroxides without concentration. When stored as a gas, these chemicals may autopolymerize as a result of peroxide accumulation.
- If a chemical from List C is inhibited, do not store it under an inert atmosphere. Oxygen is required for the inhibitor to function.
- Uninhibited chemicals from List C have a safe storage period of 24 hours.
Engineering Controls
Use a fume hood or other appropriate exhaust ventilation if an inhalation hazard is anticipated. Utilize shields, barricades, and additional PPE (such as face shields with throat protectors and heavy gloves) where there is a possibility of explosion or vigorous chemical reaction.
Work Practice Controls
- Maintain the smallest amount necessary for ongoing work.
- Purchase peroxide formers with inhibitors added by the manufacturer when possible.
- Mark the container with the date it was received and the date it was opened. If tested for peroxides, note the date it was tested.
- Do not allow materials to evaporate to near dryness unless the absence of peroxides has been shown.
- Periodically test containers with peroxide test strips. See the testing section below for more information.
- Note: some peroxide formers (including alkali metals and their amides) should not be tested with standard peroxide tests because they are both water and oxygen-reactive
Note: Never try to force open a rusted or stuck cap on a container of a peroxide-forming chemical.
Testing Procedures
There is a great deal of uncertainty regarding the concentration at which peroxides pose a hazard to researchers. Various sources suggest that the minimum hazardous concentration of peroxides in organic solution is in the range 0.005
- 1.0% (50-10,000 PPM). In most safety literature, a conservative concentration of 100 PPM peroxides is used as a control point.
By the end of the expiration date (as indicated in Table 2) for a particular peroxide forming chemical, the person using the chemical should either dispose of it or test it for peroxide content. Any container found to have a peroxide concentration greater than or equal to 100 PPM should be disposed of (call EH&S at 509-963-2338 for assistance).
Materials which are older than the suggested shelf life but have been tested and have no detectable peroxides or peroxide concentrations less than 100 PPM may be retained but should be tested at frequent intervals (see Table 2). All chemicals which are to be distilled must be tested prior to distillation regardless of age. Important note: Researchers should never test containers of unknown age or origin. Older containers are far more likely to have concentrated peroxides or peroxide crystallization in the cap threads and therefore can present a serious hazard when opened for testing. Please read section below on managing older containers.
There are several methods that are commonly used to detect for peroxides in the laboratory. Perhaps the most convenient method is the use of peroxide test strips which are manufactured by Aldrich and several other suppliers. These strips are simple to use and can be obtained from a chemical supplier. For volatile organic chemicals, the test strip is immersed in the chemical for 1 second; then the tester breathes slowly on the strip for 15-30 seconds or until the color stabilizes. The color is then compared with a colorimetric scale provided on the bottle. Strips that offer a 1-100 PPM peroxide range are useful for determining if the material is below the control point of 100 PPM. Other testing methods are available. Contact EH&S at 509-963-2252 for more information.
Safe storage period for peroxidizable chemicals:
- Unopened chemicals from the manufacturer
- Unopened chemicals from the manufacturer:12 months
- Opened containers
- Unopened chemicals from the manufacturer:12 months
- List A, Table 1 materials
- Unopened chemicals from the manufacturer:3 months
- List B, Table 1 materials
- Unopened chemicals from the manufacturer:12 months
- Uninhibited List C, Table 1 materials
- Unopened chemicals from the manufacturer:24 hours
- Inhibited List C, Table 1 materials
- Unopened chemicals from the manufacturer:12 months2
1. Never open or test containers of unknown origin or age or that have visible evidence of peroxides
2. Do not store under an inert atmosphere.
Personal Protective Equipment (PPE)
In order to select the appropriate PPE for the workplace, a Hazard Assessment is conducted. The hazard assessment determines the hazards and potential hazards associated with a task, machinery, or process. The appropriate PPE for the situation may be subsequently determined.
The Hazard Assessment Form may be found under forms on the EH&S website. It may be completed either by the workplace supervisor or the department’s Safety Officer.
Wear standard nitrile laboratory gloves (or those recommended on the SDS), lab coat, and safety glasses (meeting the requirements of ANSI/ISEA Z87.1) for all work in the laboratory.
Transportation and Storage
- Store in airtight containers in a dark, cool but not freezing, and dry area.
- Do not permit sources of heat, friction, grinding, or impact near storage areas.
- The date upon receiving and opening all incoming peroxide-forming chemicals and dispose of them immediately upon reaching their expiration date.
- Some peroxide-formers should be stored under nitrogen (or other inert gas) – consult the chemical’s SDS for more information.
Waste Disposal
Most spent, unused and expired materials are considered hazardous wastes and must be collected and disposed of within 90 days by EH&S. Contact EH&S at 509-963-2252 for waste containers, labels, manifests, waste collection, and any questions regarding proper waste disposal. Also, refer to the CWU EH&S Hazardous Waste webpage for more information.
Contact EH&S immediately to arrange for pick-up and disposal if:
- Crystals are found around the lid of the container. Do NOT attempt to open the container! or
- The container tests positive for peroxides.
Exposures/Unintended Contact
If the employee is in need of emergency medical attention, call 911 immediately.
In general, flush affected eyes or skin with water for at least 15 minutes, then seek medical attention (see below).
- Eyes: In case of contact, immediately flush eyes with plenty of water for at least 15 minutes. Remove contact lenses, if present and easy to do. Continue rinsing. Get medical aid.
- Skin: In case of contact, flush skin with plenty of water. Remove contaminated clothing and shoes. Get medical aid if irritation develops and persists. Wash clothing before reuse.
- Ingestion: If swallowed, do not induce vomiting unless directed to do so by medical personnel. Never give anything by mouth to an unconscious person. Get medical aid.
- Inhalation: If inhaled, remove to fresh air. If not breathing, give artificial respiration. If breathing is difficult, give oxygen. Get medical aid.
If there is any doubt about the severity of the injury, seek immediate medical attention.
Contact EH&S for advice on symptoms of chemical exposure, or assistance in performing an exposure assessment.
Report all work-related accidents, injuries, illnesses, or exposures to EH&S within 24 hours by completing and submitting the Injury/Illness Accident Form.
Spill Procedures
- When a spill occurs, personal safety should always come first.
- Alert and clear everyone in the immediate area where the spill occurred.
A minor (small) chemical spill is one that the laboratory staff is capable of handling safely without the assistance of safety and emergency personnel, i.e., (less than 1 Gallon or 3.5 Liters). A major/large chemical spill requires active assistance from emergency personnel.
Spill Response Steps:
MINOR CHEMICAL SPILL
- Alert people in the immediate area of the spill.
- If spilled material is flammable, turn off ignition and heat sources. Don’t light Bunsen burners or turn on other switches.
- Open outside windows, if possible.
- Use proper personal protective equipment (PPE) as indicated above.
- Avoid breathing vapors from spills.
- Confine spill to as small an area as possible.
- Do not wash spill down the drain.
- Use appropriate spill kits/sorbents to absorb the spill. Collect contaminated materials and residues and place them in the container. Contact EH&S at 509-963-2252 for proper disposal.
- Clean the spill area with water.
MAJOR CHEMICAL SPILL
Report large chemical spills (greater than 1 Gallon or 3.5 Liters) in corridors or common areas, e.g., hallways, elevators, eating areas, restrooms, offices, etc., to the University Campus Police Department at 911.
- Attend to injured or contaminated persons and remove them from exposure.
- Alert people in the laboratory to evacuate.
- If spilled material is flammable, turn off ignition and heat sources. Don’t light Bunsen burners or turn on other switches.
- Call 911 immediately for assistance.
- Close doors to the affected area.
- Post warnings to keep people from entering the area.
- Have a person available that has knowledge of the incident and laboratory to assist emergency personnel.
Report all emergencies, suspicious activity, injuries, spills, and fires to the University Campus Police Department by calling 911.
Training of Personnel
All personnel are required to complete the Chemical Hygiene Plan training. Furthermore, all personnel shall read and fully adhere to this SOP when handling the chemical.
-
Pyrophoric and Other Highly Reactive Materials SOP
Principal Investigator (PI) Approval is Required Prior to Performing this Procedure
Description
This SOP must be customized for each pyrophoric material in use in the lab. Use this section to describe the circumstances of use.
Potential Hazards
Pyrophorics are chemicals that, even in small quantities, are liable to ignite within five minutes after coming into contact with air.
Check the Safety Data Sheet (SDS) to see if the material presents other hazards, such as corrosivity, teratogenicity, water reactivity, peroxide formation, or systemic effects. If other hazards are present, appropriate safety precautions should be addressed in this SOP.
Engineering Controls
- Liquid pyrophoric should be stored in sealed containers with PTFE-lined septa to prevent air exposure, and manipulated via syringe or cannula in a chemical fume hood (over a spill tray if possible) with the sash as low as possible.
- Solid pyrophoric must be handled only in an inert atmosphere glove box or glove bag.
- Mineral oil bubblers must be used to release pressure from reagents or reaction vessels.
- Use a blast shield if available.
Work Practice Controls
Lab-specific written procedures, approved in advance by the Principal Investigator (signature required at top of customized SOP) and reviewed by EH&S (as a High-Risk Procedure), are required. These must include a designated work area (at the top of the template) and cover all sections of this template.
Before working with these compounds, read the SDS and other reference material carefully. Good web resources include:
- Sigma Aldrich Technical Bulletins AL-164 (Handling Pyrophoric Reagents) and AL-134 (Handling Air-Sensitive Reagents). Other Aldrich Technical Bulletins describe specific laboratory equipment designed for use with air- and moisture-sensitive reagents.)
- Prudent Practices in the Laboratory (National Academies Press) Sections 4.D and 6.G and Laboratory Chemical Safety Summaries for
- Butyllithiums
- Sodium (reactive metal)
- Lithium aluminum hydride
- Before purchasing pyrophoric materials, consult with EH&S at 509-963-2252 to select a compatible fire extinguisher. The extinguisher must be on hand before any work with the pyrophoric material takes place (and preferably before the material is ordered).
- Purchase minimal amounts of pyrophoric materials.
- Set up a designated area for work with pyrophoric materials – a chemical fume hood and/or a (dry) glove box (with an inert atmosphere, if needed) located within 10 seconds of an eyewash/drench hose, safety shower, and an appropriate fire extinguisher, as determined in consultation with Fire Safety.
- Incompatible materials should be removed from the area.
- A container of powdered lime or sand should be kept within arm’s reach (for covering spills).
- Employees should be aware of the location of all emergency equipment and should know how to use it if needed.
- Store and use pyrophoric chemicals under an inert atmosphere or under kerosene as appropriate.
- Know the location of the nearest compatible fire extinguisher and how to use it.
- See the above-referenced Aldrich technical bulletins for recommendations on the safe transfer of liquid pyrophorics.
- Before conducting the actual procedure, always perform a dry run (without the pyrophoric material) to identify and resolve possible safety hazards.
- Work within sight and/or hearing of at least one other person who is familiar with the hazards and written procedures.
Personal Protective Equipment (PPE)
- Wear a fully buttoned, flame-resistant lab coat (Nomex material or equivalent) with sleeves extended to the wrists, along with safety goggles and standard nitrile laboratory gloves. Leather or Kevlar gloves are recommended beneath nitrile gloves (for fire protection).
- If large quantities will be used, a chemical-resistant apron is also required. Note that personal clothing should not be of a type that may ignite (such as polyester or nylon).
Transportation and Storage
- Store and use pyrophoric chemicals under an inert atmosphere or under kerosene as appropriate.
- Store in secondary containers, away from flammables and oxidizers. (You may be able to reuse the secondary container provided by the manufacturer.)
- Avoid areas with heat, flames, and water.
- Some of these materials may need to be kept below threshold temperatures.
Waste Disposal
Waste pyrophorics should be disposed of immediately through EH&S Environmental Programs (they should NOT be allowed to accumulate). Waste must be disposed of following your laboratory-specific chemical hygiene plan and the requirements of Central Washington University’s Chemical Waste Policy and the Laboratory Chemical Waste Management Practices.
Exposures/Unintended Contact
In the case of a release of pyrophoric material, fire, or explosion in the lab, leave the area immediately and contact CWU Police by calling 911 from a campus phone. CWU Police will contact the fire department, facilities, and/or EH&S as needed.
Training of Personnel
Users must be given hands-on training for procedures/experiments involving pyrophoric or other highly reactive materials before beginning work.
Hands-on fire extinguisher training is highly recommended. Contact EH&S at 509-963-2252 for more information or to set this up.
Furthermore, training on these specific procedures must be performed by the PI or knowledgeable designee for all personnel working with pyrophoric materials and must be documented (topics covered, date, employee names, and signatures). All personnel shall read and fully adhere to the laboratory- and chemical-specific SOP for any explosives, and shall document that they have read it by signing and dating the SOP.
-
Reproductive Hazard SOP
Principal Investigator (PI) Approval is Required Prior to Performing this Procedure
Description
There are broad spectrums of chemicals that pose the potential to be a reproductive hazard. Increased recognition of the hazards associated with the transportation, operation, and storage of these materials is essential.
Potential Hazards
These chemicals have been identified as a reproductive hazard by the United Nations Globally Harmonized System of Classification and Labeling of Chemicals (GHS). Reproductive hazards are substances or agents that may have adverse effects on various aspects of reproduction including fertility, gestation/pregnancy, birth defects, lactation, genetic effects, and general reproductive performance, and can affect both women and men.
Follow prudent lab safety practices when using these chemicals. Consult with EH&S if you have any questions.
Personal Protective Equipment (PPE)
Eye protection
- Eye protection in the form of safety glasses must be worn at all times when handling reproductive hazards. Ordinary (street) prescription glasses do not provide adequate protection. Adequate safety glasses must meet the requirements of the American Standard Practice for Occupational and Educational Eye and Face Protection (ANSI Z.87. 1 1989) and must be equipped with side shields. Safety glasses with side shields do not provide adequate protection from splashes; therefore, when the potential for a splash hazard exists other eye protection and/or face protection must be worn.
- Eyewash
- Where the eyes or body of any person may be exposed to reproductive hazards, suitable facilities for quick drenching or flushing of the eyes and body shall be provided within the work area for immediate emergency use. Bottle-type eyewash stations are not acceptable.
Respiratory protection
- Fume hood
- Manipulation of reproductive hazards should be carried out in a fume hood. If the use of a fume hood proves impractical refer to the section on special ventilation.
- All areas where reproductive hazards are stored or manipulated must be labeled as a designated area.
- Glove (dry) box
- Certain reproductive hazards must be handled in a glove box rather than a fume hood. The Office of Environmental Health and Safety 509-963-2252 or the Principal Investigator will determine if this is required.
- Special ventilation
- Manipulation of reproductive hazards outside of a fume hood may require special ventilation controls in order to minimize exposure to the material. Fume hoods provide the best protection against exposure to reproductive hazards in the laboratory and are the preferred ventilation control device. When possible, handle reproductive hazards in a fume hood. If the use of a fume hood proves impractical attempt to work in a glove box or on an isolated area of the bench top.
- If available, consider using a Biological Safety Cabinet. The biological safety cabinet is designed to remove particulates (the reproductive hazard) before the air is discharged into the environment. Reproductive hazards that are volatile must not be used in a biological safety cabinet unless the cabinet is vented to the outdoors.
- If your research does not permit the handling of reproductive hazards in a fume hood, biological safety cabinet, or glove box, you must contact the Environmental Health & Safety Department at 509-963-2252.
- All areas where reproductive hazards are stored or manipulated must be labeled as a designated area.
Protective Apparel
- Lab coats, closed-toed shoes and long-sleeved clothing should be worn when handling reproductive hazards. Additional protective clothing should be worn if the possibility of skin contact is likely.
- Safety shielding
- Safety shielding is required any time there is a risk of explosion, splash hazard or a highly exothermic reaction. All manipulations of reproductive hazards which pose this risk should be performed in a fume hood with the sash in the lowest feasible position. Portable shields, which provide protection to all laboratory occupants, are acceptable.
- Gloves
- Gloves should be worn when handling reproductive hazards. Disposable nitrile gloves provide adequate protection against accidental hand contact with small quantities of most laboratory chemicals. Lab workers should contact EH&S for advice on chemical-resistant glove selection when direct or prolonged contact with hazardous chemicals is anticipated.
Safety shower
A safety or drench shower should be available in a nearby location where the reproductive hazards are used.
Signs and labels
- Doorways: The room sign must contain a Designated Area Within Caution where carcinogens, reproductive hazards, and/or acutely toxic chemicals are stored or used.
- Containers: All containers of reproductive hazards must be clearly labeled with the correct chemical name. Handwritten labels are acceptable; chemical formulas and structural formulas are not acceptable.
Vacuum protection
Evacuated glassware can implode and eject flying glass, and splattered chemicals. Vacuum work involving reproductive hazards must be conducted in a fume hood, glove box or isolated in an acceptable manner.
Mechanical vacuum pumps must be protected using cold traps and, where appropriate, filtered to prevent particulate release. The exhaust for the pumps must be vented into an exhaust hood.
Storage
Special storage
Reproductive hazards must be stored in a designated area.
Designated area
- The room sign for the laboratory must contain Designated Areas Within identifier.
- All locations within the laboratory where reproductive hazards are handled should be demarcated with designated area caution and/or posted with designated area caution signs. This includes all fume hoods and bench tops where the reproductive hazards are handled.
- Where feasible, reproductive hazards should be manipulated over plastic-backed disposable paperwork surfaces. These disposable work surfaces minimize work area contamination and simplify clean-up.
Waste Disposal
All materials contaminated with reproductive hazards should be disposed of as a hazardous waste. Wherever possible, attempt to design research in a manner that reduces the quantity of waste generated. Questions regarding waste pick-up should be directed Environmental Health & Safety Department. This office can also assist you in minimizing waste generation.
Decontamination Procedures
Personnel: Wash hands and arms with soap and water immediately after handling reproductive hazards.
Area: Decontamination procedures vary depending on the material being handled. The toxicity of some materials can be neutralized with other reagents. All surfaces should be wiped with the appropriate cleaning agent following dispensing or handling. Waste materials generated should be treated as hazardous waste.
Equipment: Decontaminate vacuum pumps or other contaminated equipment (glassware) before removing them from the designated area.
Spill Response
Anticipate spills by having the appropriate clean-up equipment on hand. The appropriate clean-up supplies can be determined by consulting the material safety data sheet. This should occur prior to the use of any reproductive hazard.
In the event of a spill, alert personnel in the area that a spill has occurred. Do not attempt to handle a spill of reproductive hazards. Vacate the laboratory immediately and call for assistance.
- Environmental Health & Safety Department 509-963-2338
- Central Washington University Public Safety Department Emergency Number 911 from a campus phone.
Remain on the scene, but at a safe distance, to receive and direct safety personnel when they arrive.
Training of Personnel
All personnel are required to complete the Chemical Hygiene Plan training. Furthermore, all personnel shall read and fully adhere to this SOP when handling the chemical.
-
Ladder Safety
The scope of this SOP is limited to portable extension and step ladders and mobile ladder stands. Other EH&S SOPs or authoritative sources must be consulted regarding permanently installed ladders, scaffolding, aerial lifts, and other devices or conditions that present a fall hazard (e.g., platforms, roofs; floor openings where it would be possible to fall from one level to another; etc.).
The main hazard associated with the use of portable ladders is falls. Falls occur for a number of reasons, including the following:
- The ladder is in poor condition or is improper for the task at hand.
- The ladder is poorly located and/or incorrectly positioned.
- The surface on which the ladder is located is slippery or uneven.
- Proper techniques are not observed when using the ladder.
The following guidelines, most of which evolve from Occupational Safety and Health Administration (OSHA) regulations, are intended to minimize the risk of falls when using portable ladders.
- Select ladders based on the anticipated use and rated load capacity.
- Load ratings, safe working height, and other safety information must be posted on the ladder by the manufacturer. This information should be replaced if it becomes worn or defaced. The rated capacity must be sufficient to accommodate the weight of the person and everything that they are carrying.
- Portable ladders are not suitable for all situations. Depending on the task at hand, an aerial lift or other device may be the better choice. For example, a portable ladder is not a good choice when it is necessary for a person to carry heavy loads or shift their center of gravity while conducting work at an elevated height; the resting point for the top of the ladder is weak or marginally secure (e.g., guttering); three points of contact cannot be maintained (two feet and one hand); the foundation/surface upon which the ladder will be placed is uneven, slippery, angled, or will otherwise make the ladder unstable; etc.
- Remember the full height of extension and step ladders is not available for use. For example, multi-section extension ladders must maintain a minimum overlap distance and extend a minimum of 3 feet past the top of the landing point. The top step and next two rungs down on a step ladder are not intended for climbing.
- Do not use portable ladders when working near (<20-feet) live electrical lines. Do not use metal ladders when working on or near electrical devices (e.g., changing light fixtures, etc.) as the ladder could become energized.
- Read and adhere to the manufacturer’s instructions.
- Do not attempt to fabricate your own ladder.
- Keep the ladder, safety feet, and auxiliary equipment in good condition at all times, and inspect them before each day’s use and after it tips over.
- Keep dry and free of oil, grease, mud, etc.
- Verify that the joint between the steps and side rails is tight, all hardware and fittings are securely attached, and movable parts operate freely without binding or undue play; rivets are secure; and side rails and rungs are free of excessive denting or other signs of wear.
- Lubricate metal bearings of locks, wheels, and pulleys frequently.
- Replace frayed or badly worn rope.
- Safety feet and other auxiliary equipment shall be kept in good condition to insure proper performance.
- Immediately remove damaged ladders from service and discard or label them as “Danger! Out- of-Service” and notify the appropriate supervisor.
- Do not use ladders as guys, braces, skids, gin poles, or for other than their intended purpose.
- Position the ladder appropriately and maintain a safe stance while on the ladder.
- Use a ladder of the proper height, as designed by the manufacturer. Do not splice or improvise to gain additional height.
- Wear proper footwear; closed-toe, sturdy, and clean.
- Inspect the area to be sure that it is free of electrical lines.
- Do not position a ladder in an area where it can be bumped or dislodged (e.g., doorway, passage, window opening, etc.). If a ladder must be located where it can be struck or displaced, secure the area by locking doors, placing barricades, having someone stand to watch, or other appropriate action.
- The foundation upon which the ladder will be placed must be even, firm, level, and not subject to skidding/slippage. Do not use blocks, rocks, boxes, or other items to “level up” or gain height. Do not use a ladder in strong winds.
- Observe the proper placement angle for extension ladders. The base of the ladder should be one foot (1 foot) out from the wall for every 4 feet of height. The side rails of an extension ladder that is used to access a higher landing must extend a minimum of 3 feet beyond that landing.
- Secure extension ladders with tie-downs or blocking of the base. If using step ladders, ensure that the ladder is fully opened and locked in place. If using a mobile ladder stand, be sure to engage the locking mechanism before climbing.
- Face the ladder while climbing and descending. Maintain three points of contact at all times on step and extension ladders. Maintain at least two points of contact (one foot and one hand) on mobile ladder stands.
- Do not lean sideways out of the ladder’s width. Do not lean so far that the naval passes outside of the ladder’s rails.
- Do not attempt to move, shift, or otherwise reposition a ladder while anyone is on it.
- Do not place any object on a mobile ladder stand in an attempt to gain additional height.
- Properly transport, store, and maintain ladders.
- Ladders should be secured while being transported in a vehicle.
- Get assistance when carrying large ladders to the work area.
- Store ladders in a sheltered area where they will not fall unexpectedly, and will not block access to hallways and fire exits.
- Wooden ladders are affected by exposure to heat and dampness. Therefore, they should be stored in a dry, well-ventilated area.
- Never paint a wooden ladder as it can hide structural defects.
- Ladders should be stored horizontally on racks or hooks with support points at the top, middle, and bottom of the ladder to prevent sagging and warping.
-
Vacuum Pump Safety
Description
This standard operating procedure outlines the handling and use of vacuum pumps. In accordance with this document, laboratories should use appropriate controls, personal protective equipment, and disposal techniques when working with vacuum pumps.
Vacuum pumps are commonly used in a variety of experimental setups to remove air and other vapors from a vessel or system. Applications that use vacuum pumps include rotary evaporators, vacuum ovens, drying manifolds, freeze-dryers, aspirators, desiccators, and filtration equipment. Many vacuum pumps use oil which can be easily contaminated and result in pump damage and hazards.
Potential Hazards
Vacuum pumps can pose chemical, mechanical, electrical, and fire hazards. Chemical exposure can occur from improper installation, trapping, and exhausting or from off-gassing of contaminated pump oil. Mechanical hazards can occur from the moving parts of the vacuum pump. Fire can result if the pump malfunctions or overheats and ignites nearby combustible materials. Electrocution can occur from faulty or defective switches and wiring.
Engineering Controls
Vacuum pumps used to evacuate systems containing toxic, volatile, or corrosive substances must be vented to the building exhaust ventilation system. Whenever possible locate the pump in a vacuum pump cabinet or a ventilated cabinet. Ensure that pumps have belt guards. Traps such as a cold trap should be used in line with high vapor loads to minimize the amount of volatile chemicals being evacuated and reaching the pump oil. Ensure the cold trap is appropriate for the situation and follows all manufacturer and safety guidelines.
Work Practice Controls
General:
- Place the pump on a spill tray to contain oil spills if the equipment fails.
- Shield any glassware under a vacuum.
Physical:
- Ensure all vacuum pump belt systems are guarded.
- Electrical cords and switches must be free from defects.
- Avoid placing pumps in an unventilated and enclosed receptacle.
- Do not operate pumps near combustible materials.
- Use the correct vacuum tubing and replace the old tubing.
Chemical:
- Use engineering controls to avoid exposure.
- Ensure pump oil is compatible with vapors that will pass through the pump (i.e. avoid hydrocarbon pump oil and oxidizing gases/vapors).
- Close the valve between the vessel and the pump before turning off the pump to avoid introducing oil into the system.
- Ensure gases or vapors will not damage the pump.
- If cold traps are used, check for blockage.
- Check oil levels and change the oil when necessary. Change oil when it begins to turn a dark brown color.
- An oil mist separator can be used to prevent oil loss.
Personal Protective Equipment (PPE)
Wear safety glasses, lab coat, long pants, close-toed shoes, and gloves when performing all vacuum operations.
Transportation and Storage
Vacuum pumps must be stored on spill trays to prevent oil spills. Vacuum pump areas may be insulated for noise, if necessary.
Waste Disposal
All used vacuum pump oils must be disposed of through EH&S.
Do not dispose of chemical wastes by dumping them down a sink, flushing them in a toilet, or discarding them in regular trash containers. Contact EH&S at (509)-963-2252 or at EHS@cwu.edu for waste containers, labels, waste collection, and any questions regarding proper waste disposal. Also, refer to EH&S’s Hazardous Waste webpage for more information.
Exposures/Unintended Contact
If the employee is in need of emergency medical attention, call 911 immediately. Report all work-related accidents, injuries, illnesses, or exposures to Labor & Industries (L&I) within 24 hours by contacting 800- 423-7233.
Contact EH&S for advice on symptoms of chemical exposure, or assistance in performing an exposure assessment.
Complete the EH&S Online Accident Reporting Form or Report an Unsafe Condition or Hazard Report form.
Spill Procedure
A minor (small) chemical spill is one that the laboratory staff is capable of handling safely without the assistance of safety and emergency personnel, i.e., less than 1 Gallon or 3.5 Liters. A major/large chemical spill requires active assistance from emergency personnel.
For small oil spills, treat the oil as a hazardous chemical spill. Use appropriate absorbents and dispose of them as hazardous waste. For large oil spills contact EH&S at (509) 963-2338.
- When a spill occurs, personal safety should always come first.
- Alert and clear everyone in the immediate area where the spill occurred.
Additional Spill Response Steps:
MINOR CHEMICAL SPILL
- Alert people in the immediate area of the spill.
- If spilled material is flammable, turn off ignition and heat sources. Don’t light Bunsen burners or turn on other switches.
- Open outside windows, if possible.
- Wear protective equipment, including safety goggles, gloves, and a long-sleeve lab coat.
- Avoid breathing vapors from spills.
- Confine spill to as small an area as possible.
- Do not wash spill down the drain.
- Use appropriate spill kits/sorbents to absorb the spill. Collect contaminated materials and residues and place them in the container. Contact EH&S (509) 963-2252 for proper disposal.
- Clean the spill area with water.
MAJOR CHEMICAL SPILL
- Attend to injured or contaminated persons and remove them from exposure.
- Alert people in the laboratory to evacuate.
- If spilled material is flammable, turn off ignition and heat sources. Don’t light Bunsen burners or turn on other switches.
- Call Central Washington University’s Public Safety at 911 immediately for assistance.
- Close doors to the affected area.
- Post warnings to keep people from entering the area.
- Have a person available that has knowledge of the incident and laboratory to assist emergency personnel.
CWU News

Online Master’s of Education program now offers special education endorsement
May 15, 2024
by Rune Torgersen

Lenny Price brings Detroit perspective to CWU Jazz
May 15, 2024
by University Relations